
뉴스페이스 3D 프린팅 로켓 엔진 개발 동향
Copyright Ⓒ The Korean Society of Propulsion Engineers
This is an Open-Access article distributed under the terms of the Creative Commons Attribution Non-Commercial License(http://creativecommons.org/licenses/by-nc/3.0) which permits unrestricted non-commercial use, distribution, and reproduction in any medium, provided the original work is properly cited.
초록
발사체 분야에서 3D 프린팅 로켓 엔진은 뉴스페이스 활동에 있어서 주요 초점이 되어왔다. SpaceX는 그들의 로켓 엔진, 즉, Falcon 9의 Merlin과 Dragon 모듈에 3D 프린팅 부품을 사용한 최초의 업체였다. 현재 Rocket Lab은 전자빔 프린팅 방식을 사용하여 효율적으로 Rutherford 엔진을 생산하여 소형 위성 전용 발사 서비스를 일상적으로 제공하고 있다. 추진제 탱크의 로봇 제조로 잘 알려진 Relativity Space도 PBF 프린팅 방식으로 제작된 Aeon 1 엔진의 비행을 앞두고 있다. 최근 공중 발사 시스템을 입증한 Virgin Orbit도 3D 프린팅 로켓 엔진을 개발했습니다. 한국에서는 KARI 소형발사체연구부에서 금속 3D 프린팅 기술을 사용하여 소형 로켓 엔진용 추력 챔버를 제작하고 개발했다.
Abstract
In launch segment, 3D printed rocket engines have been a focal point of the new space activities. SpaceX was the first company to use 3D-printed parts for their rocket engines, Falcon 9’s Merlin and Dragon modules. Rocket Lab now routinely provides a dedicated launch service for smallsats due to efficient production of their Rutherford engine with an E-beam type printing method. Relativity Space well-known for their robotic manufacturing of propellant tanks is also about to fly their Aeon 1 engines built out of a PBF-type printing method. Virgin Orbit who recently proved their air launch system had also developed a 3D printed rocket engine. In Korea, KARI Small Launcher R&D Office built and tested thrust chambers for small rocket engines using metal 3D printing technology.
Keywords:
New Space, 3D Printing, Additive Manufacturing, Methane Engine, Kerosene Engine키워드:
뉴스페이스, 3D 프린팅, 적층제조, 메탄 엔진, 케로신 엔진1. 서 론
적층제조(additive manufacturing, AM)라고 불리는 3D 프린팅 기술은 국방기술, 항공우주기술, 의료기술 등 많은 분야에서 적용되고 있다. 특히 재생냉각채널과 분사기 등 복잡하고 정밀한 형상이 요구되는 발사체 엔진 분야를 중심으로 3D 프린팅 수요가 늘어나고 있다. 발사체 엔진과 같은 정밀한 부품을 제작하기 위해서는 DED(Directed Energy Deposition)와 같이 분말(약 80 μm급)과 와이어 등을 제작품에 직접 녹이면서 분사하여 층별로 쌓는 방식보다는 PBF(Powder Bed Fusion)와 같이 미세한 분말(약 40 μm급)을 챔버 내에 얇은 층으로 도포하고, 레이저나 전자빔을 사용해 녹여서 제작하는 방식이 더 적합하다. 그러나 PBF는 그 제작 공정상 챔버 안에 들어가는 사이즈의 제품만을 개발할 수 있고, 따라서 발사체 소형 엔진 부품만 개발할 수 있었다[1].
SpaceX의 Raptor 엔진 부품 등 발사체 엔진 부품에 적층제조가 활발하게 사용되기 시작하면서 PBF 장비가 발사체 엔진에 맞게 축방향으로 길어지는 대형 장비가 나타나기 시작했다. EOS의 자매회사인 AMCM에서 축방향 길이가 1 m 급인 M4K 제품을 출시하면서 로켓엔진 대형부품에 대한 수요를 만족시키기 시작했고, Velo3D에서도 Sapphire XC 1MZ를 출시하면서 600 mm 직경의 제품을 1 m 급으로 프린팅이 가능하면서 대형 사이즈의 3D 프린팅 엔진에 대해서도 경쟁구조가 형성되게 되었다. 상업적으로 우주 분야에 이용 가능한 3D 프린터가 늘어남에 따라 신생 로켓 및 부품 제조업체의 수는 급증하고 있으며, Strategic Market Research에 따르면 전 세계 항공우주 3D 프린팅 시장규모는 2030년까지 92억 7천만 달러에 이를 것으로 예상하고 있다[2].
본 연구에서는 뉴스페이스 시대에 기존의 방식에서 점차 3D 프린팅으로 로켓 엔진의 개발 방향이 바뀌는 동향들에 대해서 조사하였으며, 국내에서 개발되고 있는 3D 프린팅 메탄 엔진에 대해서 서술하였다.
2. 뉴스페이스 업체들의 AM 엔진 개발
2.1 SpaceX
SpaceX의 Elon Musk는 자신들이 로켓 엔진에서 가장 먼저 3D 프린팅을 사용했다고 주장하였는데, 이미 2013년에 PBF 방식 중 하나인 EOS사의 DMLS(Direct Metal Laser Sintering)를 사용하여 산화제 주 밸브V(Main Oxidizer Valve, MOV)의 하우징을 제작하였다고 공개하였다(Fig. 1).
SpaceX의 최초 3D 프린팅 제품인 MOV는 2014년 1월에 Falcon 9 로켓 1단의 9개 엔진 중 하나의 엔진에 적용되어 THAICOM 6 임무와 Orbital Science의 GEO Star 2 위성의 임무를 위해서 발사되었다. 이것은 Falcon 9의 v1.1 모델로서 Falcon 9가 재사용을 하기 위해 착륙용 랜딩 레그(landing leg)가 장착되기 전의 마지막 모델이었다. Merlin 1D가 Octaweb 방식으로 처음으로 부착되었던 Falcon 9 v1.1의 세 번째 모델부터 AM을 사용한 MOV가 장착되었기 때문에, Merlin 1D의 비교적 초기 모델부터 AM이 적용되었음을 알 수 있다. 프린팅된 밸브 하우징은 기존에 주조로 제작된 부품보다 강도, 파괴 저항성, 연성이 모두 우수한 것으로 나타났으며, 재료 물성치에 대해서도 변동성이 낮은 것으로 나타났다[4]. SpaceX에서는 몇 개월이 걸리던 밸브 하우징 제작을 단지 이틀만에 프린팅할 수 있어 제작 속도에서 우위를 보였다고 밝혔다. 본 모델은 3D 프린팅 부품으로 궤도 발사(orbital launch)에 성공한 첫 케이스라고 할 수 있다.
이와 동시에 SpaceX는 유인 우주선 드래곤(Dragon)에 사용될 비행 하드웨어를 3D 프린팅으로 제작하기 위해 3년 동안 기술개발을 해왔으며, 2013년 말에 초합금인 인코넬로 제작한 SuperDraco 엔진 챔버를 DMLS를 사용하여 3D 프린팅 하였다(Fig. 2). SpaceX 사내에서 설계 및 프린팅 제작된 SuperDraco는 엔진당 6.9 MPa의 연소압에서 72.6 kN(16,000 lb)의 최대 추력을 내며, 추력을 20%∼100% 범위에서 깊은 추력제어(deep throttle)가 가능하고, 다중 점화, 연소시간 연장, 극도의 비공칭 조건에서의 추진제 흐름에도 불구하고 정상적인 작동이 가능하였으며, 80번 이상의 연소 시험을 진행하여 신뢰성도 입증되었다. 3D 프린팅을 사용하여 기존의 기계 가공에 비해 제작에 소요되는 리드타임이 10배나 단축되었다고 밝혔으며, 첫 번째 개념설계부터 최초 연소 시험까지 3개월이 약간 넘게 걸리는 놀라운 속도로 설계와 제작을 할 수 있었다고 밝혔다. 드래곤 두 번째 버전에서 SuperDraco 8기를 4면에 부착하여 발사체에 비상사태가 발생하는 경우 우주 비행사를 헬리콥터와 같은 정확도로 안전하게 수송할 수 있게 하기 위해 최대 12만 파운드의 축추력을 발생시켜서 탈출 후 착륙할 수 있도록 도움을 주게 된다. 2014년 말의 발사 탈출 시스템에서 SuperDraco를 비행시험하였고, 2020년 유인우주선 Crew Dragon의 비상착륙 시스템에 적용되었다[4].
SpaceX는 2016년 화성으로 가기 위한 ITS (Interplanetary Transport System)라고도 불리는 스타십(Starship)을 개발하기 위한 메탄 전-유동 다단연소 사이클(Full-flow staged combustion cycle) 엔진 랩터(Raptor, Fig. 3)를 발표하였다. 그리고 이 엔진은 질량 기준 약 40%가 3D 프린팅 기술을 사용하여 제작할 것으로 밝혔다[7]. 그들은 Merlin과 SuperDraco 엔진에서 이미 3D 프린팅이 많이 입증되었다고 하면서, 기존 방식으로 불가능했던 경량 부품의 생산이 가능해져서 생산 비용을 크게 절감하고, 엔진의 추력 대 중량비를 높일 수 있다고 하였다. 그리고 3D 프린팅 엔진 구성품은 설계 변경시 업데이트된 사양을 재주조(re-casting)하는데 몇 주 또는 몇 달을 소비하는 대신 짧은 시간 안에 구현해 낼 수 있다고 하였다. 그래서 랩터의 추진제 밸브, 터보펌프 부품 및 인젝터 시스템의 많은 구성요소들이 프린팅 제품으로 구성되어 있다고 밝혔다[8]. 2021년까지 SpaceX는 메탄 엔진 랩터의 주요 부품을 생산하기 위해서 Velo3D의 사파이어(Sapphire) 제조 시스템 22대를 캘리포니아 호손(Hawthorne)에 있는 SpaceX 본사(headquarter)로 주문하였으며, SpaceX에서는 랩터 엔진의 어떤 부품을 제작하는지 밝히지는 않았지만, 서포트 프리(SupportFree)와 같은 Velo3D의 기술들이 터보펌프 개발을 용이하게 하기 때문에, 터보펌프 부품들을 주로 프린팅하는 것으로 추정하고 있다[9]. 2022년 11월에 SpaceX는 Raptor 엔진을 하루에 1개씩 생산하는데 성공했다고 NASA 부국장 Mark Kirasich가 밝혔기 때문에[10], Velo3D의 사파이어 제조 시스템 22대로 양산되는 랩터 엔진 부품들은 랩터 1기당 프린팅으로 빌드(build)하는데 걸리는 시간이 22일 이내일 것으로 추정할 수 있으며, 10%의 마진을 고려한다면 약 20일 정도일 것으로 추정할 수 있다.
2.2 Rocket Lab
Rocket Lab은 엔진의 대부분의 부품을 3D 프린팅으로 제작한 발사체로 궤도에 투입하는데 성공한 최초의 기업이다. 전기펌프 공급 3D 프린팅 엔진이라는 새로운 개념으로 빠른 속도로 엔진을 개발할 수 있었고, 2017년 최초로 궤도에 투입하는 것을 시도하였고 2018년 최초로 3D 프린팅 엔진을 사용하여 위성을 궤도로 투입하는데 성공하였으며, 2022년 6월 28일 NASA의 Cislunar Autonomous Positioning System Technology Operations and Navigation Experiment(CAPSTONE) 미션을 수행하기까지 26회의 발사이력으로 발사업계의 선도적인 경쟁자로서 발돋움하게 되었다[11]. 지상추력 24 kN, 지상 비추력 311초의 Rutherford 엔진(Fig. 4)은 추진용 밸브(prop valve), 분사기, 펌프, 엔진 챔버들을 PBF의 일종인 Electron Beam Melting (EBM) 기술을 사용하여 프린팅 후 생산되었다. CEO 피터 백(Peter Peck)은 적층제조 기술을 사용하기 위해서 로켓 설계에 근본적인 변화를 주기 시작했고, 모든 분사기를 3D 프린팅하고, 내부 형상을 정교하게 조절할 수 있어 다른 공정에서는 할 수 없는 탁월한 혼합과 우수한 성능이 가능하였다고 밝혔다[13].
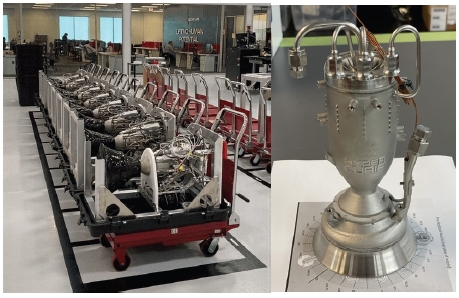
The 3D printed Rutherford engines (left) and HyperCurie thruster (right) of Photon for Capstone Mission[11,12].
Capstone 미션은 Rocket Lab 뿐 아니라 NASA의 저비용 탐사 미션에서도 중요한 이정표를 달성하였다. Rocket Lab은 자신들의 Photon 우주선을 통해 NASA가 달 미션에 필요한 평균 비용의 일부에 불과한 1천만 달러 미만의 비용으로 달탐사를 수행할 수 있음을 입증해 보였다. 일례로 2018년, NASA 우주 망원경 TESS를 달 궤도로 보내기 위해서 SpaceX의 Falcon 9 로켓을 이용하였는데, 이를 위해 NASA는 8700만 달러를 지불하였다. Photon 우주선은 이중 추진제(bipropellant)를 사용하여 120 N의 추력을 공급하는 3D 프린팅으로 제작된 HyperCurie(Fig. 4)라는 추력기를 사용하였다[11].
Rocket Lab은 2021년에 Electron 다음 단계의 대형 메탄 재사용 발사체로 Neutron 로켓을 설계하고 있다고 발표하였으며 2022년 9월 21일에 Neutron을 위한 산화제 과잉 다단연소 사이클 엔진 Archimedes(Fig. 5)를 발표했다. 이 엔진은 지상엔진의 진공비추력이 329초 이고 최대 추력이 730 kN(165 klbf)이며, 고공엔진의 경우 진공비추력이 367초 이고, 최대추력 890 kN(200 klbf)로 설계하였다고 하였다. 지상엔진은 50%의 추력조절이 가능하게 설계할 예정이며, 약 2.1 m의 높이라고 발표했다. SpaceX의 Falcon 9과 같이 1단에 9개의 Archimedes 엔진을 배치하고 2단에 1개의 Archimedes 고공엔진을 배치하여 Neutron을 개발하고 있다. 엔진은 3D Printing을 사용해서 제작하고자 하는 대형 엔진인 만큼 DMG MORI 의 Lasertec 125 DED 하이브리드 적층/가공 장비를 사용하여 제작하는 것으로 발표했다[14].
2.3 Relativity Space
Relativity Space는 엔진뿐만 아니라 발사체의 추진제 탱크까지 WAAM(Wire Arc Additive Manufacturing) 기술을 사용하여 발사체의 95% 이상을 3D 프린팅으로 제작하고자 하는 목표를 가지고 2015년에 설립되었다. Stargate라는 대형 WAAM 프린터를 구축하고 추진제 탱크 뿐 아니라 페어링부까지 프린팅 기술을 사용하여 제작하고 있으며 최초로 제작한 발사체 Terran 1 전체 질량의 85%를 적층제조로 제작하고 있다. 또한 Terran 1 발사체를 개발하면서 9개의 메탄 3D 프린팅 엔진 Aeon 1을 1단에, 1개의 진공형 Aeon 1을 2단에 부착하여 궤도에 투입하는 SpaceX의 Falcon 9과 Rocket Lab의 Electron 발사체의 공식을 충실히 따르고 있다. Relativity는 AI 소프트웨어 기반의 제조방식과 3D 프린팅 기술력 때문에 100배나 적은 부품으로 60일 만에 로켓을 완성할 수 있다고 주장하고 있다[15].
Aeon-1 엔진은 지상에서 100 kN(23 klbf), 고공에서 113 kN(25.4 kblf)의 추력을 가진 가스발생기형 메탄 엔진이며, PBF 중 Selective Laser Sintering(SLS) 방식과 DMLS 방식을 사용하여 100개 이하의 부품들로 제작되었다[16]. 연소기 챔버 소재를 초기에 3D Systems의 DMP 500을 사용하여 니켈기반 합금으로 제작했다가 후에 구리합금으로 변경했다. 초기에 Rocket Lab과 같이 니켈기반 합금으로 챔버를 제작한 이유는 제조 과정 중에서 작업하기 용이했기 때문이라고 밝혔다. 하지만 구리합금 기반의 엔진은 열전도성이 좋아 더 높은 온도에서 챔버를 동작할 수 있기 때문에 높은 연소효율이 가능하여 구리챔버로 변경하기로 하였다. 니켈 챔버를 구리챔버로 변경하지 않아도 되었지만, 향후 Terran R에 적용할 고성능 대형 엔진을 위해 구리 챔버를 프린팅하여 시험하기로 하였다. 적층 제조를 이용하여 소재를 변경해서 프린팅하는 것은 비교적 간단한 작업이었고, 2022년 초에 구리챔버로 변경하여 테스트 스탠드에 장착해 시험을 수행하여 단 5일 만에 full duration 시험(Fig. 6)을 마쳤다고 CEO인 Ellis가 밝혔다[17]. 2022년 2월까지 Aeon 1 엔진에 대해서 니켈기반 AM 챔버를 포함하여 500회 이상의 시험이 수행되었으며, 7월에는 9개의 엔진이 클러스트링 된 Terran 1 로켓의 1단 시험이 수행되었고[15], 2023년 3월에 처음으로 Terran 1이 시험발사 되었다.
Relativity Space는 Terran 1보다 20배나 무거운 탑재체를 궤도에 투입할 수 있는 완전 재사용 발사체 Terran R을 2024년에 발사하는 것을 목표로 하고 있으며, 이를 위해 1.1 MN(250 klbf)의 대형 메탄 가스발생기 엔진인 Aeon R을 3D 프린팅을 사용하여 개발하기로 하였다[18]. Aeon R은 110톤급 엔진으로서 현재까지 3D 프린팅으로 제작 예정된 엔진 중 가장 큰 엔진으로 평가받고 있다. 2022년 8월 Relativity의 CEO인 Ellis는 Aeon R을 위해 프린팅되고 있는 제품을 공개하였는데(Fig. 7), Velo3D의 Sapphire XC 1MZ에서 생산된 제품으로 추정되는 거대한 구리챔버였다[19]. 기존 PBF 프린팅 머신은 공간의 제약이 많았으며, 소재의 제약도 많았으나, 이것들을 극복한 대형 프린터들이 경쟁적으로 나타나기 시작하면서 사이즈의 한계를 극복한 대형 엔진들을 적층할 수 있게 되었다. 물론 대형 엔진의 확대노즐부까지 PBF 프린터로 적층하는 것은 현재까지는 불가능한 상황이지만, 프린팅 기술의 진보로 새로운 로켓 엔진의 개발은 계속 촉진되고 있다.
2.4 Ursa Major Technologies
2015년에 창립된 Ursa Major Technologies는 다른 발사체 업체들과는 달리 로켓 추진 시스템 개발에만 집중하는 미국 유일의 민간업체이다. 그들은 케로신 기반의 산화제 과잉 다단연소 사이클 엔진을 DMLS를 사용한 3D 프린팅 기반으로 개발하기 시작하여 80% 이상의 부품을 프린팅으로 대량 생산하였다. 22 kN(5,000 lbf)의 추력을 가진 Hadley는 2022년 중순까지 50기 이상을 콜로라도주 Berthoud 본사에서 제작하고 36,000초 이상을 시험하였으며, 2022년 말까지 30기를 출하할 예정을 가지고 있다[20,21].
Ursa Major의 두 번째 3D 프린팅 엔진인 Ripley는 현재 개발이 진행되고 있으며(Fig. 8), Hadley와 같이 니켈 기반 3D 합금을 연소기 챔버 소재로 프린팅하는 대신 구리합금을 사용하여 2022년 7월에 EOS M400 프린터를 통해 적층 제작되었다. Ursa Major는 2021년 10월에 오하이오 주 Youngstown에 미국 연방하원의원 Tim Ryan과 국방부가 지원하는 제조 혁신 연구소 America Makes의 연방 재정 지원 300만 달러로 Advanced Manufacturing Lab을 새롭게 구축하였고, 이곳에서 Ripley 개발을 위해 3D 프린팅 공정에 대한 혁신을 수행하고 있다. 새롭게 개발된 프로세스를 통해서 기존 제조 방식으로 최소 6개월이 소요되는 생산 및 배송 주기를 1개월로 단축하여 제작하는데 성공하였다. Ripley는 Hadley와 마찬가지의 산화제 과잉 케로신 다단연소시스템으로 구성되어 있으며, 2021년까지 156 kN(35 klbf)으로 설계했다가 시장 수요를 충족하기 위해 최근 222 kN(50 klbf)의 추력 엔진으로 신속하게 재설계하였다고 하였다[20].
Ursa Major의 고객은 여러 업체가 있는데, Hadley 엔진은 미 공군 연구소(Air Force Research Lab.)의 공중발사체 X-60A의 추진시스템용으로 2020년에 시험이 수행되었다. 또한, 세계에서 가장 큰 비행기에서 발사될 수 있도록 설계된 프로토 타입 극초음속 발사체 개발에 착수한 미국 항공우주 업체인 Stratolaunch와 계약을 체결하였으며, 2020년 10월말 Stratolaunch는 발사체에 마하 5 이상을 공급할 수 있는 Ursa Major의 Hadley 엔진 시험을 완료하였다고 밝혔다. 또한 Phantom Space라는 초소형위성 발사체 신생업체에 엔진을 공급하기로 하였고, Phantom Space는 그들의 로켓의 1단에 Ursa Major 엔진 7개, 2단에 1개를 사용하여 제작할 것을 언급하였다[23].
Ursa Major는 그들의 세 번째 대형 엔진으로 2021년 초까지 Samus라는 220 kN(50 klbf)의 추력을 가진 수소 엔진을 개발하다가 2021년 중반에 Arroway(Fig. 9)라는 890 kN(200 klbf)의 추력을 가진 메탄 다단연소 사이클 엔진을 개발하는 것으로 방향을 전환했다. Arroway 엔진은 2023년에 초기 연소시험을 수행할 예정이며, 2025년부터 납품이 가능할 것으로 예상하고 있다. 특히 Arroway는 현재 공급부족에 부딪힌 러시아 RD-180, RD-181 엔진을 대체할 수 있는 옵션 중 하나로 검토되고 있으며. 산화제 과잉 다단연소 사이클을 사용하는 Rocket Lab의 Archimedes 엔진과 블루 오리진의 BE-4 엔진과는 달리 연료 과잉 다단연소 사이클 시스템으로 개발되고 있다. Ursa Major는 그동안 케로신 엔진 개발에서 메탄 엔진 개발로 방향을 전환한 이유로 메탄이 더 깨끗하게 연소되고 효율이 높으며, 케로신보다 비용이 저렴하기 때문이라고 하였다. 그리고 엔진 출시 업계에서 재사용성을 최적화할 수 있는 아키텍처 옵션을 제공할 수 있기 때문이라고 밝혔다[24].
2.5 Launcher Space
Livestream과 Mevo의 창업가인 Max Haot가 2017년에 설립한 Launcher Space는 3D 프린팅 기술에 의한 저비용 고효율 엔진을 강조하며 소형 위성을 궤도에 진입시키는 비용을 낮추려 하는 기업이다. 원래 Launcher의 목표는 자체로켓을 만들어 다른 소형 발사체 업체들과 경쟁하는 것이었고, 초기에 설계했던 Rocket-1은 5개의 E-2 엔진을 사용해 773 kg을 지구 저궤도에 실을 수 있었지만, 2021년부터 Launcher Light라는 보다 더 작은 발사체를 사용하여 150 kg의 탑재체를 지구 저궤도에, 105 kg의 탑재체를 태양동기궤도에 올리는 것으로 목표를 변경하였다. Launcher Light는 1단에 E-2 엔진 1개, 2단에 E-1 고공용 엔진 1개, 3단에 Launcher Orbiter용 추력기 1개로 이루어져 있다. 2017년 2.2 kN(500 lbf) 급 E-1 엔진의 연소기를 인코넬로 프린팅하여 엔진 개발을 처음으로 시작했던 Launcher는 2018년에 E-1 엔진을 Cu-Cr-Zr 합금을 사용하여 EOS M290으로 프린팅하여 뉴욕 롱아일랜드 시험장에서 시험하기 시작했고, 2019년에 당시 최대 높이의 프린터인 AMCM의 M4K를 사용하여 높이 860 mm, 출구 노즐 직경이 410 mm의 당시 세계 최대의 3D 싱글 프린팅 챔버인 10톤급 추력을 가진 E-2(Fig. 10)를 프린팅하여 제작하는데 성공했다.
2020년부터 미시시피의 NASA Stennis Space Center에서 E-2 엔진의 연소기 시험과 터보펌프 시험을 시작했고, 2021년 1월 중순에 CEO인 Max가 자신이 보유하고 있던 Mevo 카메라 회사를 로지텍에 넘기면서 본사를 기존 뉴욕 브루클린에서 SpaceX Hawthorne 본사 근처의 Daphne 거리에 본사를 이전하여 본격적으로 Launcher Light를 개발하기 시작했다[25].
Launcher Light는 3단에 에탄-아산화질소를 사용하는 1.1 kN(250 lbf)의 추력기를 3D 프린팅으로 출력하여 사용하는데, 이것은 SpaceX Falcon 9의 라이드 쉐어로 사용할 수 있도록 ESPA Grande 24’‘ 표준 분리 시스템 규격으로 인터페이스를 제작했다. 1단과 2단에 사용하는 케로신-액체산소 시스템을 탑재했을 때 라이드 쉐어에서 발생될 수 있는 문제를 줄이기 위해 상온 보관이 가능한 추진제를 사용하였으며, 제작 비용을 감소하기 위해 Orbiter에 사용되는 티타늄 추진제 탱크와 1.1 kN(250 lbf) 인코넬 추력기(Fig. 11)는 Velo3D의 Sapphire를 사용하여 프린팅하였다. 또한 E-2 엔진의 터보펌프 부품인 인듀서, 임펠러, 하우징 등도 이 프린터를 사용하여 제작하고 있다. Launcher Orbiter의 첫 번째 발사는 2023년 1월 초에 Cape Canaveral에서 Falcon 9의 라이드 쉐어 미션인 Tranporter-6로 이루어졌다[26].
2.6 Orbex
2015년에 Moonspike Ltd.라는 이름으로 설립되고 2016년 Orbical Express Launch Ltd. 줄여서 Orbex라고 변경한 이 영국의 소형발사체 회사는 500 km 태양 동기 궤도에 150 kg의 탑재체를 상업발사하는 것을 목표로 하는 Prime이라는 발사체를 개발하고 있다. Prime에 사용되는 액체산소와 프로판으로 구동되는 액체로켓 엔진은 1단에 6기, 2단에 1기가 들어간다. Prime에 사용되는 엔진의 이름과 추력규모는 알려져 있지 않으나 니켈 기반의 소재를 사용하여 3D 프린팅하는 것은 공개하였다. Prime의 이륙중량이 18톤으로 공개되었기 때문에, 엔진의 추력 규모는 약 4톤급 정도로 추정되어 Launcher E-2보다는 작고 Rocket Lab의 Rutherford보다는 큰 사이즈라고 할 수 있다. 2019년에 SLM Solutions의 SLM-800으로 프린팅하였다고 공개한 엔진(Fig. 12)은 2019년 2월 단일 부품(Single-piece)로 만든 가장 큰 3D 프린팅 로켓 엔진이라고 발표하였으나 일주일 만에 더 큰 Launcher의 E-2 엔진의 단일 프린팅 부품의 발표로 자신들의 주장이 무색해졌다[27,28].
2021년 Launcher가 E-2 엔진 연소기 개발을 위해서 사용했던 AMCM M4K 장비를 생산성 향상을 위해 추가적으로 도입한 Orbex는 연간 35개 이상의 엔진 부품을 프린팅할 수 있다고 밝혔다. BioLPG라고 하는 독특한 형태의 연료를 사용하는 이 엔진은 탄소 중립에 대해서 기존의 케로신 기반 엔진에 비해 불완전 연소 가스를 최대 86% 까지 줄일 수 있다고 주장했다[28]. 2022년 4월 자신들의 3D 프린팅 엔진을 구리합금으로 변경했다고 밝혔는데, 기존의 니켈기반 소재에서 자신들이 기대했던 성능과 전체 임무시간(full duration)이 나오지 않은 것으로 보인다. AMCM M4K 장비를 통하여 Launcher와 같이 구리합금 챔버를 단일 부품으로 프린팅한 것으로 보이며, Prime을 재사용 발사체로 개발하려고 한다고 하지만, 현재까지 공개된 자료로는 많은 시험이 이루어졌다고 보기 어렵다[29].
2.7 Virgin Orbit
Virgin Orbit은 3D 프린팅 연소실을 제작하는 것과 관련하여 일찍부터 NASA와 협력관계에 있었고, 알라바마 헌츠빌에 있는 Marshall Space Flight Center와 클리블렌드에 있는 Glenn Research Center, 그리고 캘리포니아의 에드위즈에 있는 Armstrong Flight Research Center와 협력하여 3D 프린팅 엔진을 제작하고 시험하였다[30]. NASA는 2014년에 3D 프린팅 용도로 개발된 GRCop-84 분말을 사용하여 프린팅을 진행하였고 2018년 말과 2019년 초에 Virgin Orbit 엔지니어와의 협력을 통해서 8.9 kN(2,000 lbf)의 소형 고압 액체산소/케로신 엔진을 시험했다. 이러한 기술들을 기반으로 Virgin Orbit에서는 연소기 챔버의 내피 부품은 DMLS를 이용한 PBF 방식을 채택하여 제작하였고, 외부 재킷은 DED 방식의 일종이라고 할 수 있는 클래딩(cladding)을 사용하여 구조적으로 엔진 구성품들의 성능을 향상시키면서 비용, 리드 타임, 복잡한 부품들의 개수를 줄일 수 있었다고 하였다[31]. 특히 PBF로 구리챔버를 제작한 후에 후가공하고 이후 이어지는 적층제조 기술인 DED를 적용하기 위해서 Virgin Orbit은 DMG Mori와 제휴하였으며, Long Beach에 있는 제조 본사에 투자하여 그들의 LauncherOne에 사용하는 엔진 제작을 자동화하는 일에 힘쓰고 있다. 2021년에 LauncherOne의 연소기를 DMG Mori의 최신 2세대 첨단 제조장비(Fig. 13)에서 제작하기 시작하였으며, 적층제조를 포함한 엔진 생산에서 생산속도를 가속화시키고, 자동화시키기 위해 노력하고 있다고 밝혔다[32].
2.8 Pangea Aerospace
스페인의 Pangea Aerospace는 다른 로켓 엔진 개발 업체와는 다른 컨셉인 에어로스파이크 엔진을 3D 프린팅으로 개발하고 있다. 에어로스파이크 엔진은 대부분의 벨 노즐(bell nozzle)을 갖춘 엔진에 비해 지상과 고공에서 대기압의 변화에 상관없이 유리한 성능특성을 보일 수 있다는 장점을 가지고 있다. 1950년대에 벨 노즐형 엔진을 대체할 수 있는 강력한 개념으로 인식되었고, 1980년대와 1990년대에 NASA에 의해서 테스트되었지만, 당시 사용가능한 제조 및 재료 기술의 한계로 잘 개발되지 못하였다. Pangea Aerospace는 3D 프린팅의 장점인 미세 채널 구조의 자유도를 높일 수 있다는 것을 최대한 활용하였고, 추진제로 사용하는 액체 메탄을 하우징 부 냉각에 액체 산소를 내부의 스파이크(또는 플러그라고 하기도 함) 부에 이중으로 냉각유체로 투입시킨다는 아이디어를 가지고 20 kN급 에어로스파이크 엔진인 DemoP1을 제작하여 시험하였다[33].
DemoP1(Fig. 14)은 액체 산소와 액체 메탄으로 구동되는 세계 최초의 적층제조된 에어로스파이크 로켓 엔진이라는 타이틀을 가지게 되었고, 전통적으로 직사각형 슬롯 형태로 제작되었던 재생냉각채널을 냉각효율을 극대화하고 열피로를 최소화하기 위해 적층제조를 사용하여 채널 구조를 나선형 구조로 다른 평면에 인공적인 곡률을 도입하였고, 이러한 나선형 구조는 원심 작용에 의해 벽에 냉각수를 밀어넣어서 열전달 효율을 극대화시켰다. 3D 프린팅 부품은 표면마감이 좋지 않다는 것이 잘 알려져 있는데 Pangea는 파트너사인 Aenium과 협력하여 빌드 과정에서 거칠기 수준을 수정하였고, 중요한 영역에서는 오버행 각도를 조절하여 거칠기를 활용한 냉각성능 향상에도 활용하였다. 또한 복잡한 내부 채널 형상구조는 분말을 제거하기 어렵게 되어 있는데, 이를 해결하기 위해서 여러 분말 제거 구멍을 구조에 통합시켰으며, 다양한 후처리 작업을 통해서 분말을 제거하였다[33].
최근 EOS는 적층제조용 크롬-니오븀 구리합금 분말인 GRCop42를 400 W 이하의 낮은 레이저 출력에서도 프린팅하는 것에 성공하였으며, 이러한 기술들을 활용하여 Pangea와 Aenium은 GRCop42 기반으로 자신들의 DemoP1 엔진을 프린팅하였다. GRCop42는 C18150(CuCrZr) 및 순수 구리(OFHC)와 같은 다른 AM 인증 구리합금과 비교할 때 고온에서 뛰어난 열전도율과 크리프 강도 등의 기계적 성질을 가지고 있어 C18150에 비해 사용 온도에서 다시 상온으로 온도가 내려왔을 때에도 안정적으로 입계(grain) 크기와 강도를 유지한다고 하고 있다. 2022년 현재 GRCop42는 C18150에 비해서 TRL 9급의 프린팅 프로세스가 개발된 것은 아니지만, Aenium사는 자신들의 레이저 시스템 및 AM에 대한 응용 재료 과학 지식을 기반으로 다중 볼륨 레이저 에너지 밀도(M-VLED)라는 방법을 사용해 프린팅을 수행하였다. 이 방법을 통하여 금속간 화합물을 생성하거나 희석시키고, 일부 상 또는 미세 구성 화합물들을 나타나게 하거나 제거하거나 하여 특정 영역의 기계적/열적 특성을 복셀(voxel) 단위로 변경시킬 수 있다고 하였다. 이로 인해 항복강도, 인장강도, 연신율, 열전도율, 경도, 표면 거칠기, 잔류응력 등을 복셀 단위로 프로그램화하여 특정부위의 열교환 효과를 생성하거나 비전도성 쉘(shell)을 만들고, 다양한 저사이클 열피로(Low-cycle thermal faitgue) 강도를 증가시키며, 부품 전반에 걸친 잔류응력 제어를 할 수 있다고 하였다[33].
Pangea Aerospace는 DemoP1 에어로스파이크 엔진 시험을 독일 Lampoldshausen에 있는 P8.2 고압 시험시설에서 수행하였으며, 7번의 수류시험과 10번의 연소시험을 수행하였다고 밝혔다. Pangea도 재사용 엔진을 염두에 두고 개발하고 있기 때문에 저사이클 피로를 유발하는 온도 구배를 측정하면서 시험을 수행하였다. 이후 Pangea는 이 시험을 기반으로 Arcos라는 큰 팽창비를 사용하고 터보펌프를 환상형 에어로스파이크 내부에 배치한 상용 엔진개발을 시작했다[33].
3. 국내 AM 엔진 개발
3.1 국내 메탄 AM 엔진 개발
2022년 10월까지 국내의 발사체 뉴스페이스 스타트업에서는 3D 프린팅을 사용하여 엔진을 개발하지 않고 있으며, 항공우주연구원 소형발사체연구부를 중심으로 적층제조 엔진 연소기가 개발되고 있다. 2019년에 처음으로 메탄 3톤급 연소기 실린더부 3D 프린팅 제작을 시작으로 3톤급 연소기의 헤드부, 노즐목부가 차례로 PBF 방식을 사용하여 Inconel 소재로 제작되었다. 또한 2020년부터 메탄 1톤급 연소기가 역시 PBF 방식을 사용하여 구리합금과 Inconel 소재로 각각 제작되었으며, 2020년 말부터 1톤급 연소기 챔버의 시험을 시작하였다[34]. 2022년에는 3톤급 연소기의 저압 시험을 10회 이상 수행하는데 성공하였다. 이후 국내 DED 장비 제작 업체 인스텍(InssTek)을 통하여 연소기 챔버의 내피를 구리합금, 외피를 니켈 기반 합금의 이종소재로 제작하는데 성공하였으며, 2023년에 연소시험을 수행하였다.
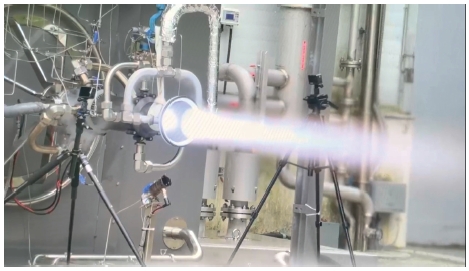
A low pressure combustion test of the 3 tonf-class methalox engine AM chamber made by powder bed fusion.
또한 SpaceX가 Falcon 9에 적용한 방식인 1단에 9개 엔진을 사용하고 같은 엔진을 2단에 1개 적용하는 재사용 발사체 모델을 사용하여 국내 사정에 적합한 재사용 발사체, 정지궤도 발사체, 소형 지상 발사체, 소형 공중 발사체를 개발한다고 하였을 때 35톤급 메탄 다단연소 사이클 엔진이 적합하다는 것들을 기존의 연구[35-38]에서 밝혔으며, 3D 프린팅을 이용하여 35톤급 메탄엔진 연소기를 니켈 기반의 소재를 사용하여 개발하고 제작하는 연구가 항공우주연구원과 비츠로넥스텍에서 현재 진행되고 있다.
3.2 국내 케로신 AM 엔진 개발
국내 케로신 엔진 부품에도 적층제조 방식이 일부 적용되었으며, 한국형발사체 7톤급 엔진용 산화제 개폐밸브를 일부 AM을 사용하여 제작할 수 있음을 보여주었다. 터보펌프의 일부 부품들도 AM을 사용하여 제작하는 것에 대한 시도가 있었다[1]. 고성능 케로신 가스발생기형 로켓 엔진을 위해서 일체형 배플분사기를 Inconel 625 소재로 항공우주연구원에서 개발하여 시험하였는데, 이를 통하여 고추력 대형 엔진에서 발생하는 배플 연소기의 열내구성 저하 방지가 가능한 연소기 헤드부를 제작할 수 있는 주요 적층제조 공정을 개발하는데 성공하였다[39]. 또한 상단에 사용할 수 있는 9톤급 케로신 다단연소사이클 엔진의 터빈부와 가스덕트부를 3D 프린팅을 이용해서 제작하는 연구가 진행되었으며, 일부 시험이 진행되었다[40].
4. 결 론
SpaceX, Rocket Lab, Relativity Space, Ursa Major Technologies, Launcher Space, Orbex, Virgin Orbit, Pangea Aerospace에서 적용하고 확대하고 있는 3D 프린팅 로켓엔진 개발 동향을 살펴 보았으며, 다음과 같은 결론을 얻을 수 있었다.
- (1) 로켓엔진 개발에서 AM의 적용은 점차 확대되어 가고 있으며 AM 장비 업체들의 품질이 좋아지고 대형화되어감에 따라 소형엔진에 적용되던 AM 기술이 대형엔진에도 점차 적용되어 가고 있다.
- (2) 로켓 엔진 개발에 주로 사용되는 AM 기술은 정밀한 채널 및 인젝터 제작이 가능한 PBF 기술이며, 각 엔진 개발 업체는 자신들과 협력 가능한 3D 프린팅 업체들과 긴밀하게 제휴하여 3D 프린팅 설계, 제작 기술을 개발해가면서 엔진을 제작하고 있다.
- (3) AM 기술을 주로 사용하여 발사에 성공한 업체는 현재까지는 Rocket Lab이 유일하고, 일부 적용하여 발사에 성공한 업체로는 SpaceX, Virgin Orbit이 있으며, 2022년 11월 현재 Relativity Space가 발사를 기다리고 있다.
- (4) 기존에 케로신 엔진을 개발한 이후 AM 기술을 주로 활용하여 최근 메탄엔진으로 변경한 업체는 SpaceX, Rocket Lab, Ursa Major이며, 처음부터 메탄엔진을 AM으로 개발했던 업체는 Relativity Space, Pangea Aerospace이고, 케로신 엔진을 AM으로 개발하는 업체는 Launcher, Virgin Orbit이다.
Acknowledgments
[이 논문은 한국추진공학회 2022년도 추계학술대회(2022.11.23.∼25, 파라다이스호텔 부산) 발표논문을 심사하여 수정ㆍ보완한 것임.]
References
-
Lee, K.O., Lim, B., Kim, D.J., Hong, M. and Lee, K., “Technology Trends in Addtively Manufactured Small Rocket Engines for Launcher Applications,” Journal of the Korean Society of Propulsion Engineers, Vol. 24, No. 2, pp. 73-82, 2020.
[https://doi.org/10.6108/KSPE.2020.24.2.073]
- Schwaar, C., “3D-Printed Rockets Set To Blast Off,” Forbes, retrieved 30 Jun. 2022 from https://www.forbes.com/sites/carolynschwaar/2022/06/30/3d-printed-rockets-set-to-blast-off/?sh=37e98c9b2b6a, .
- “The Future of Design,” SpaceX, retrieved 6 Sep. 2013 from https://www.youtube.com/watch?v=xNqs_S-zEBY, .
- “SpaceX Reveals 3D-Printed Rocket Engine Parts,” retrieved 19 Aug. 2014 from https://www.designnews.com/design-hardware-software/spacex-reveals-3d-printed-rocket-engine-parts, .
- “SpaceX SuperDraco inconel rocket chamber w regen cooling jacket emerges from EOS 3D metal printer,” Elon Musk twitter, retrieved 6 Sep. 2013 from https://twitter.com/elonmusk/status/375737311641628672, .
- “The first Raptor Vacuum engine (RVac) for Starship has shipped from SpaceX’s rocket factory in Hawthorne, California to our development facility in McGregor, Texas,” SpaceX, retrieved 4 Sep. 2020 from https://twitter.com/SpaceX/status/1302038129990279168, .
- Belluscio, A.G., “ITS Propulsion – The evolution of the SpaceX Raptor engine,” NASA Spaceflight.com, retrieved 3 Oct. 2016 from https://www.nasaspaceflight.com/2016/10/its-propulsion-evolution-raptor-engine/, .
- “SpaceX Raptor,” Spaceflight, retrieved 30 Oct. 2022 from https://spaceflight101.com/spx/spacex-raptor/, .
- Zafar, R., “SpaceX’s 3D Manufacturing Systems Supplier For Raptor Engine To Go Public Through SPAC Deal,” retrieved 23 Mar. 2021 from https://wccftech.com/spacexs-3d-manufacturing-systems-supplier-for-raptor-engine-to-go-public-through-spac-deal/, .
- Burger, E., “SpaceX is now building a Raptor engine a day, NASA says,” Arstechnica, retrieved 2 Nov. 2022 from https://arstechnica.com/science/2022/11/spacex-is-now-building-a-raptor-engine-a-day-nasa-says/, .
- Listek, V., “Rocket Lab’s 3D Printed Engine Powers NASA CAPSTONE Satellite Mission,” 3D Print.com, retrieved 29 Jun. 2022 from https://3dprint.com/292360/rocket-labs-3d-printed-engine-powers-nasa-capstone-satellite-mission/, .
- “Another set of 3D printed Rutherford engines rolling off the line in Long Beach. We’re fast approaching our 200th engine!,” Rocket Lab, retrieved 13 May 2020 from https://twitter.com/rocketlab/status/1260710472820523009, .
- Winick, E., “Rocket Lab: The small firm that launched the 3D-printed space revolution,” MIT Technology Review, retrieved 19 Jun. 2019 from https://www.technologyreview.com/2019/06/19/134877/rocket-lab-the-small-firm-that-launched-the-3d-printed-space-revolution/, .
- “2022 Inverster Day and Neutron Update,” Rocket Lab, retrieved 21 Sep. 2022 from https://s28.q4cdn.com/737637457/files/doc_presentations/2022/09/Final_Investor-Day-Presentation-2022_Sept-21.pdf, .
- Robinson-Smith, W., “Relativity Space nears launch of first 3D-printed rocket,” Spectrum News 13, retrieved 17 Aug. 2022 from https://www.mynews13.com/fl/orlando/news/2022/08/17/relativity-space-nears-launch-of-first-3d-printed-rocket, .
- Sher, D., “Relativity’s fully 3D printed Terran 1 rocket to launch in summer 2022,” 3D Printing Media Network, retrieved 9 Jun. 2022 from https://www.3dprintingmedia.network/relativitys-fully-3d-printed-terran-1-rocket-to-launch-in-summer-2022/, .
- Burger, E., “Relativity Space printed its Terran 1 rocket’s second stage in a few weeks,” Arstechnica, retrieved 24 Mar. 2022 from https://arstechnica.com/science/2021/03/relativity-space-printed-its-terran-1-rockets-second-stage-in-a-few-weeks/, .
- “New Agreement With NASA Puts Reality Space on Path to Operate One of America’s Largest Rocket Engine Test Facilities,” Relativity Space, retrieved 18 Oct. 2022 from https://www.relativityspace.com/press-release/2022/10/18/new-agreement-with-nasa-puts-relativity-space-on-path-to-operate-one-of-americas-largest-rocket-engine-test-facilities, .
- “250,000+ pounds thrust 3D printed Aeon R chamber - newest iteration. Development pace increasing and lots more hardware showing up at @relativityspace. Gonna be a beast of an engine,” Tim Ellis, retrieved 25 Aug 2022 from https://mobile.twitter.com/thetimellis/status/1562924690980671489, .
- Johnson, O., “Ursa Major’s Advanced Manufacturing Lab in Youngstown, Ohio Delivers its First 3D-Printed Rocket Engine Components,” Ursa Major, retrieved 12 Jul. 2022 from https://www.ursamajor.com/blog/ursa-majors-advanced-manufacturing-lab-in-youngstown-ohio-delivers-its-first, .
- Johnson, O., “Ursa Major delivers its first copper-based 3D printed engine components,” TCT Magazine, retrieved 15 Jul. 2022 from https://www.tctmagazine.com/additive-manufacturing-3d-printing-news/latest-additive-manufacturing-3d-printing-news/ursa-major-delivers-its-first-copper-based-3d-printed-engine/, .
- “Ripley, Redefining Small to Medium Class Launch,” Ursa Major, retrieved 5 Nov. 2022 from https://www.ursamajor.com/engines/ripley, .
- Listek, V., “Startup Accelerator: Ursa Major is 3D Printing Rocket Engines to Grow Space Economy,” 3D Print.com, retrieved 28 Jan. 2021 from https://3dprint.com/278184/startup-accelerator-ursa-major-is-3d-printing-rocket-engines-to-grow-space-economy/, .
- “Ursa Major presents project for largely 3D printed Arroway rocket engine,” 3D Printing Media Network, retrieved 3 Jun. 2022 from https://www.3dprintingmedia.network/ursa-major-completes-new-and-largely-3d-printed-arroway-rocket-engine/, .
- Essop, A., “Launcher Sets Test Fire Date For Rocket Engine with Largest 3D Printed Combustion Chamber,” 3D Printing Industry, retrieved 15 Nov. 2019 from https://3dprintingindustry.com/news/launcher-sets-test-fire-date-for-rocket-engine-with-largest-3d-printed-combustion-chamber-164820/, .
- “Launcher Set to Trailblaze with 3D Printed Space Rockets,” All3DP, retrieved 27 May 2022 from https://all3dp.com/4/launcher-set-to-tailblaze-with-3d-printed-space-rockets/, .
- Tubbesing, K., “Orbex manufactures rocket engine with 3D printer,” Honnover Messe, retrieved 25 Feb. 2019 from https://www.hannovermesse.de/en/news/news-articles/orbex-manufactures-rocket-engine-with-3d-printer, .
- “Orbex biofuel space rocket,” Vabio, retrieved 26 Nov. 2021 from https://uabio.org/en/materials/11856/, .
- “More test firings of Orbex´s fully 3D-printed engines,” Orbex, retrieved 7 Apr. 2022 from https://orbex.space/news/more-test-firings-of-orbex-s-fully-3d-printed-engines, .
- Rowe, J., “NASA and Virgin Orbit 3D Print, Test Rocket Combustion Chamber,” NASA, retrieved 15 May 2019 from https://www.nasa.gov/centers/marshall/news/news/releases/2019/nasa-and-virgin-orbit-3d-print-test-rocket-combustion-chamber.html, .
- “How Virgin Orbit is using 3D printing to push boundaries of orbital class rockets,” TCT Magazine 3D Printing & Additive Intelligence, retrieved 10 Dec. 2020 from https://www.tctmagazine.com/additive-manufacturing-3d-printing-industry-insights/aerospace-insights/how-virgin-orbit-is-using-3d-printing/, .
- “In the Pursuit of Manufacturing Excellence,” VirginOrbit, retrieved 10 Sep. 2021 from https://virginorbit.com/the-latest/in-the-pursuit-of-manufacturing-excellence/, .
- “Making the unmakeable: How metal AM is bringing the aerospike rocket engine to life,” retrieved 10 Sep. 2022 from https://www.metal-am.com/articles/making-the-unmakeablehow-3d-printing-is-bringing-the-aerospike-rocket-engine-to-life/, .
-
Lim, B., Kim, C., Lee, K.O., Lee, K., Park, J., Ahn, K., Namkoung, H.J. and Yoon Y., “Development Trends of Liquid Methane Rocket Engine and Implications,” Journal of the Korean Society of Propulsion Engineers, Vol. 25, No. 2, pp. 119-143, 2021.
[https://doi.org/10.6108/KSPE.2021.25.2.119]
- Lee, K.O., Kim, D.J., Park, S.Y. and Lee, K., “An Analysis of Strategies of Engine Development of SpaceX,” 51th KSPE Fall Conference, Busan, Korea, pp. 249-257, Dec. 2018.
-
Lee, K.O., “An Analysis of Launch Vehicle Development Strategy of SpaceX,” Journal of the Korean Society of Propulsion Engineers, Vol. 23, No. 6, pp. 72-86, 2019.
[https://doi.org/10.6108/KSPE.2019.23.6.072]
-
Lee, K.O., Lee, J., Park, S.Y., Roh, W.R., Im, S.H., Nam, K.W. and Seo, D., “Korean Reusable Launch Vehicle Development Strategy Using SpaceX’s Strategy,” Journal of the Korean Society of Propulsion Engineers, Vol. 25, No. 3, pp. 101-112, 2021.
[https://doi.org/10.6108/KSPE.2021.25.3.101]
-
Lee, K.O., Seo, D., Lim, B., Lee, J., Park, J.S., Choi, S. and Lee, K., “Falcon 9 Type Korean RLV and GTO-LV Mission Design,” Journal of the Korean Society of Propulsion Engineers, Vol. 26, No. 3, pp. 32-42, 2022.
[https://doi.org/10.6108/KSPE.2022.26.3.032]
- Kim, S.K., Han, S., Joh, M, Kim, J., Lee, B.Y., Ryu, C., Choi, H.S., Noh, Y.O. and Cho, H.R., “Development of Integrated Baffle Injectors Using Additive Manufacturing for High-Performance Liquid Rocket Engine,” 52th KSPE Fall Conference, Busan, Korea, KSPE 2020-2301, Nov. 2020.
- Cho, N.K., Woo, S.P., So, Y.S., Lee, J.H., Lee, S.J., Jeon, J.S., Hwang, C.H., Lee, K.J., Kim, S.H. and Han, Y.M., “Status of Preceding Development of Staged Combustion Cycle Engine,” Current Industrial and Technical Trends in Aerospace, Vol. 19, No. 1, pp. 119-132, 2021.