
Jet A-1 연료의 열전달 특성에 관한 실험적 연구
Copyright Ⓒ The Korean Society of Propulsion Engineers
This is an Open-Access article distributed under the terms of the Creative Commons Attribution Non-Commercial License(http://creativecommons.org/licenses/by-nc/3.0) which permits unrestricted non-commercial use, distribution, and reproduction in any medium, provided the original work is properly cited.
초록
본 논문에서는 재생냉각 연소기에서 냉각제 및 연료로 사용되는 Jet A-1의 열전달 특성에 대해 실험적으로 연구하였다. 냉각채널 가열을 위한 인가 전류, 모사 시편 지름, 시편 후단 압력, Jet A-1 유속을 변화시키며, 시편에서의 벽면 온도 및 시편 전/후단에서의 Jet A-1 온도를 측정하였다. 시편 지름과 유속이 열전달 특성에 중요한 인자임을 알 수 있었으며, 시편의 후단 압력은 열전달 성능에 영향을 주지 않음을 확인할 수 있었다. 열전달 실험결과는 기존 Nu수 경험식들과 비교하였으며, 최종적으로 새로운 Nu수 경험식을 도출하였다.
Abstract
In this paper, the heat transfer characteristics of Jet A-1, which is used as a coolant and fuel in a regeneratively cooled thrust chamber, were experimentally studied. By varying the applied current for heating the cooling channel, the simulated specimen diameter, the specimen outlet pressure and the coolant flow rate, the wall temperatures of the specimen and the Jet A-1 temperatures at the specimen inlet/outlet were measured. It was found that the specimen diameter and the flow rate were important factors for the characteristics of heat transfer and the outlet pressure did not affect the performance of heat transfer. The results of the heat transfer experiments were compared with the previous Nusselt number empirical equations and novel Nusselt number empirical equations were finally derived.
Keywords:
Regenerative Cooling Channel, Jet A-1, Heat Transfer, Electrical Heating System, Nusselt Number키워드:
재생냉각채널, 항공유, 열전달, 전기적 가열 시스템, 넛셀 수1. 서 론
액체로켓엔진, 스크램제트와 같은 추진기관의 연소기는 고온, 고압의 연소가스로 인해 열유속이 매우 높은 환경에 노출된다. 따라서 연소실 벽면에 발생할 수 있는 열적/구조적 손상을 방지하기 위해 적절한 냉각이 필수적이다. 액체로켓엔진 연소기는 재생냉각(regenerative cooling), 막냉각(film cooling), 용융냉각(ablative cooling), 배출냉각(dump cooling), 침투냉각(transpiration cooling), 복사냉각(radiation cooling) 등을 복합적으로 이용하고 있다[1]. 재생냉각에서 추진제는 연소실 냉각채널을 따라 흘러 벽면을 냉각한 후 분사기를 통해 연소실로 분사된다. 냉각과정에서 회수한 열은 엔탈피를 재사용하는 것이므로 높아진 연소효율을 기대할 수 있다[1,2].
재생냉각채널 설계 및 해석을 위해서는 냉각제로 사용되는 추진제의 열전달 특성을 알아야 한다. 이를 위해 해외의 많은 연구자들이 전기적 가열 방식을 활용하여 냉각채널 내부의 추진제 열전달 특성을 모사한 실험을 수행하였다[3]. Liang 등[4]은 메탄, 프로판, 로켓 케로신에서의 코킹 발생 특성을 확인하고, 각 연료의 열전달 성능에 대한 새로운 Nu수 경험식을 제안하였다. Zhong 등[5]은 2단계 가열기 시스템을 도입하여, China no. 3 케로신에 대한 코킹 실험을 수행하였다. 그들은 임계 압력 조건에서는 임계 온도 근처에서 열전달 성능이 향상됨을 관찰하였으며, Nu수 경험식을 도출하여 기존의 케로신 경험식들과 비교하였다. Wang 등[6]은 원형단면과 사각단면 관(tube)에 인위적인 거칠기를 주어, 높은 열유속과 초임계 조건에서 케로신의 열전달을 연구하였다. 적절한 표면 거칠기가 압력 손실은 증가시키지만 열전달 성능은 향상시키는 것을 발견하였다. Linne 등[7]은 재질이 다양한 금속 관과 구리 관을 브레이징(brazing) 용접하여 시편을 제작하였고, 전기적 가열 방식을 이용하여 JP-7 연료의 열전달 특성과 열적 안정성에 대한 연구를 수행하였다. 실험결과를 선행 연구의 경험식들과 비교하였으며, 현미경으로 튜브 내부를 관찰하여 코킹 발생 여부를 확인하였다.
국내에서도 케로신 열전달, 열분해에 관한 연구는 몇 차례 수행되었다. Park 등[8]은 스테인리스강 관에서 Jet A-1의 강제대류 열전달 특성에 대해 연구하여, Jet A-1의 입구 온도가 열전달 특성에 중요하다는 것을 확인하였다. 또한 수정된 Nu수 관계식을 제시하여, 기존의 경험식들과 비교하였다. Lim 등[9]은 코킹 현상을 정량적으로 평가하기 위해 연료 가열실험을 수행하였으며, 탄화수소 연료와 관 재질인 구리합금의 적합성을 검토하였다. Jeon 등[10]은 냉각채널, 연소실, 노즐을 2차원 축대칭으로 가정하여 재생냉각의 유동장과 열전달에 대한 수치해석을 수행하였으며, 채널 내부 유량과 형태에 따라 냉각제의 온도 변화가 달라짐을 확인하였다. Park[11]은 액체로켓엔진 재생냉각에 많이 사용하는 RTE 코드를 대체하기 위한 열해석 코드 개발을 진행하였다. Seo[12]는 열전달이 반경 방향으로만 이루어진다는 가정 하에 액체로켓엔진의 재생냉각 열전달 과정을 모사하였다.
한국형발사체 액체로켓엔진에 추진제 및 냉각제로 Jet A-1이 사용되지만, 국내에서는 아직도 다양한 벽면 온도를 갖는 구리 관 내에서 Jet A-1의 열전달 특성에 대한 실험 데이터가 충분치 않은 상황이다. 따라서 본 논문에서는 재생냉각채널 설계 및 해석을 위한 보다 실질적인 데이터를 확보하고자 높은 열유속 조건에서 Jet A-1의 열전달 특성을 연구하였다. 이를 위해 내부 구리와 외부 스테인리스강으로 이루어진 냉각채널 모사 시편을 제작하였으며, 인가 전류, 모사 시편 지름, 시편 후단 압력, Jet A-1 유속을 변수로 열전달 실험을 수행하였다.
2. 관련 이론 및 적용
Fig. 1은 실험에서 사용한 냉각채널 모사 시편과 열전달 방식을 간단히 나타낸 개략도이다. 일정한 열유속이 냉각채널 시편에 가해지는 있다면, 열유속은 Eq. 1과 같이 케로신의 유량, 비열, 채널을 통과하는 케로신의 온도 변화, 그리고 단면적으로 표현할 수 있다. 열전달이 이루어지는 단면적(A)은 시편 중심에서 케로신이 맞닿는 내부면적이기 때문에 Eq. 2와 같이 구리 내경(di)과 시편 길이(L)로 표현된다.
(1) |
(2) |
일정하게 공급되는 전류는 시편을 저항체로 하여 열량으로 변환되고, 열은 전도에 의해 시편 외벽에서 내벽으로 전달되므로 Eq. 3과 같이 나타낼 수 있다.
(3) |
시편 내벽에서 케로신으로의 강제대류 열전달은 다음 식으로 계산할 수 있다.
(4) |
이상적인 조건에서는 다음 식이 성립된다[8].
(5) |
위 식들을 통해 측정된 외부 벽면 온도로부터 케로신과 맞닿는 내부 벽면 온도를 계산하고, 결국 길이 방향으로 대류 열전달계수(hl,b)를 구할 수 있게 된다. 본 실험에서는 시편의 길이가 260 mm로 짧고 제작성의 문제 때문에, 길이 방향으로 평균된 대류 열전달계수를 사용하였다. 따라서 시편 내 케로신의 평균 포용 온도(bulk temperature)는 Eq. 6으로, 케로신의 이론적인 Nu수는 Eq. 7로 정의하였다.
(6) |
(7) |
시편 내 포용 온도와 압력을 기준으로 케로신의 물성값[13]을 이용하여, 무차원수인 Re수와 Pr수를 계산하였다.
(8) |
(9) |
3. 실험장치 및 방법
3.1 냉각채널 모사 시편
냉각채널 내 케로신 열전달 특성에 대한 실험을 위하여 Fig. 2와 같은 냉각채널 모사 시편을 설계, 제작하였다. 시편은 내피(구리 관, UNS C10100)와 외피(스테인리스강 관, UNS S31603)를 브레이징을 통해 일체형으로 제작하였다. 외부 스테인리스강 관의 내경은 4 mm, 외경은 10 mm를 갖는다. 반면 내부 구리 관의 경우 외경은 모두 4.0 mm로 동일하나, 내경은 1.6, 2.0, 2.4 mm로 제작되었다. 전체 시편 길이 300 mm중 가열되는 부분의 길이 L = 260 mm이다. 가열 부위 전 입구 길이의 길이대 직경비는 10 이상으로, 가열 영역 내 유동은 완전 발달(fully developed)될 것으로 판단되었다. 가열 부분에 총 6개의 열전대를 설치할 수 있도록 설계하였고, 냉각제 유동 방향에 따라 열전대에 번호를 부여하였다. 내피 구리 관의 외부 벽면 온도를 정확하게 측정하기 위해 노출형 K-type 열전대를 사용하였으며, 비드 부분이 구리 관 외부에 접하여 실험 중 떨어지지 않도록 록피팅(lok fitting)으로 고정하였다.
3.2 실험장치
실험장치 개략도를 Fig. 3에 나타내었다. 실험장치는 크게 냉각채널 모사 시편, 케로신 공급탱크와 배수탱크, 고압공기 공급탱크, 열교환기, 정류기, 계측장비로 이루어졌다.
고압공기 공급탱크에 연결된 레귤레이터를 이용하여 일정한 압력으로 케로신을 가압하였으며, 시편 전단과 후단에 니들밸브를 설치하여 유량과 냉각채널 후단에 걸리는 압력을 조절하였다. 시편 전/후단에 압력센서(Sensys, PSH)와 온도센서를 배치하여 케로신 압력 및 온도의 변화를 계측하였으며, 시편 전단에 설치된 터빈 유량계(Kometer, NK-250)와 온도센서를 이용하여 측정된 부피 유량을 질량 유량으로 환산하였다. 실험조건에 따라 시편을 지난 케로신은 온도가 매우 높아져 자연 발화될 가능성이 있기 때문에 상수도 물로 냉각하는 열교환기를 사용하여 온도를 낮춘 후 케로신 배수탱크로 회수되도록 하였다. 시편이 설치되어 있는 부분은 시험 도중 파손에 의한 사고를 방지하기 위해 주변을 투명한 강화 플라스틱 상자로 덮었으며, 고온 케로신의 유출로 인한 발화를 방지하기 위해 상자 내부에 기체질소를 지속적으로 공급하였다. 실험조건 변경 및 직경에 따라 시편을 교체하는 경우 시편 전단에 있는 퍼지(purge) 밸브를 열어주어 시편 내부 케로신을 모두 제거하였다.
가열하기 위해 사용한 정류기(220 V, 3상)는 최대 5000 A × 10 V (50 kW)로 시편에 가해지는 전류를 수동으로 조절하였다. 가열 시 인가 전류와 시편 재료의 저항으로 인해 공급되는 전압이 정류기 패널에 표시되고 이를 기록하였다. 계측장비를 통해 측정되는 실험 데이터는 모두 NI-cDAQ를 이용하여 100 Hz의 샘플링 속도로 저장하였다.
3.3 실험조건
물질 변화 과정 중 초임계로 천이되는 구간에서 발생하는 비등(boiling)은 열전달 성능에 도움이 될 수 있고, 임계압력 이상에서는 물질의 뚜렷한 상변화가 발생하지 않는다[14,15]. 하지만 케로신의 압력이 임계압력보다 낮은 경우, 비등 현상이 나타나면 액체 케로신이 기체로 변해 국부적으로 열이 방출되지 못하여 시편이 파손될 수 있다[16]. 케로신의 임계압력은 대략 20∼25 bar이기 때문에[17], 시편 후단 압력을 30 bar, 50 bar 조건으로 설정하였다.
시편 내 유속 조건은 10, 20 m/s으로 고정하였다. 실험을 수행하기 전에 상용 CFD 프로그램인 CFX로 수치해석을 수행하여 시편 벽면 온도가 500 K을 넘지 않도록 실험조건을 설정하였다. 그리고 물성이 잘 알려진 물을 이용한 열전달 예비실험을 통해 시편에 전달되는 온도, 실험장치의 기능, 발생하는 압력손실, 유량 및 온도센서의 정확도 등을 확인하였다. 시편 직경과 케로신 유동 속도에 따라 500∼3000 A 범위에서 인가 전류를 조절하였다. 시편 전/후단의 밸브를 조절하여 후단 압력과 케로신 유속 조건을 맞춘 뒤, 정류기를 가동하여 시편을 가열하였다. 자세한 실험조건은 Table 1에 정리하였다.
4. 실험 결과
본 연구에서는 내경이 1.6, 2.0, 2.4 mm인 냉각채널 모사 시편을 사용하였다. 구체적으로 내경이 1.6 mm인 시편에서 20번, 2.0 mm인 시편에서 18번, 2.4 mm인 시편에서 13번의 열전달 실험이 수행되었다. 정류기 가동 후 시편에 가해지는 열량으로 인해 시편 벽면 온도와 케로신 포용 온도가 급격히 상승한 후 크게 변하지 않는 지점까지 실험을 수행하였다. 이는 실험결과 분석 시 최대한 정상상태(steady state)에 근접한 데이터를 사용하기 위함이었다.
4.1 실험 데이터
Fig. 4는 내경(di) 2.0 mm 시편에서 유속(v) 20 m/s, 인가 전류(I) 2000 A 조건일 때 측정된 온도 분포를 시편 후단 압력(Poutlet)에 따라 나타낸 그래프로, 후단 압력에 따라 온도 변화 차이가 거의 없다는 것을 보여준다. Jet A-1은 T1 전단에서부터 냉각제 역할을 수행하면서 T6 후단 지점을 통과하기까지 지속적인 열유속을 받는다. 이러한 열교환 때문에 길이 방향으로 열유속이 일정하다면 T1에서 T6로 갈수록 벽면 온도가 증가하여야 한다. 하지만 Fig. 4(a)와 (b) 모두 T2의 온도가 T3 온도보다 조금 더 높게 계측되었다. 이렇게 이론적 예상과 약간 다른 이유는 시편 가공 시 기술적 제약으로 인해 구리 관의 두께가 균일하게 제작되지 못한 영향이라고 생각된다.
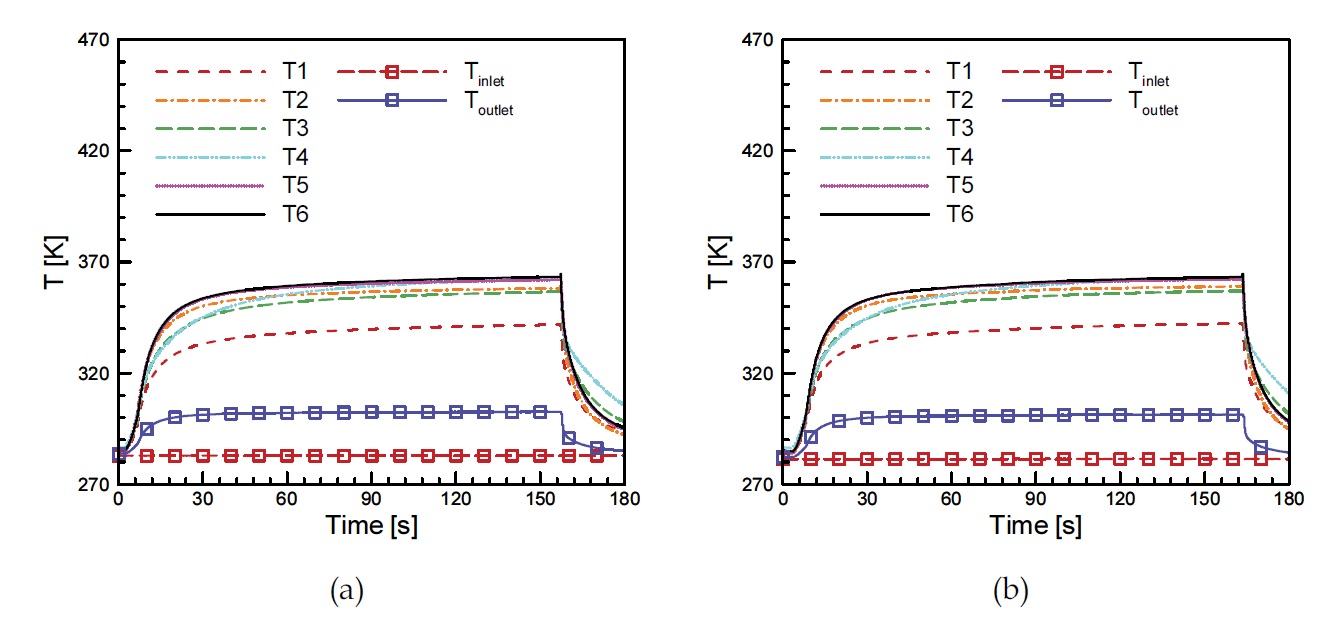
Specimen wall and kerosene temperature distribution with time at di = 2.0 mm, v = 20 m/s, I = 2000 A, and Poutlet = (a) 30 bar and (b) 50 bar.
Fig. 5는 내경이 2.0 mm인 시편에서 유속 20 m/s, 후단 압력 30 bar 조건일 때 측정된 온도 분포를 인가 전류에 따라 나타낸 것이다. 전류가 증가하면 시편에 가해지는 열량이 증가하므로 Tinlet을 제외한 나머지의 온도가 상승하는 것을 확인할 수 있다.
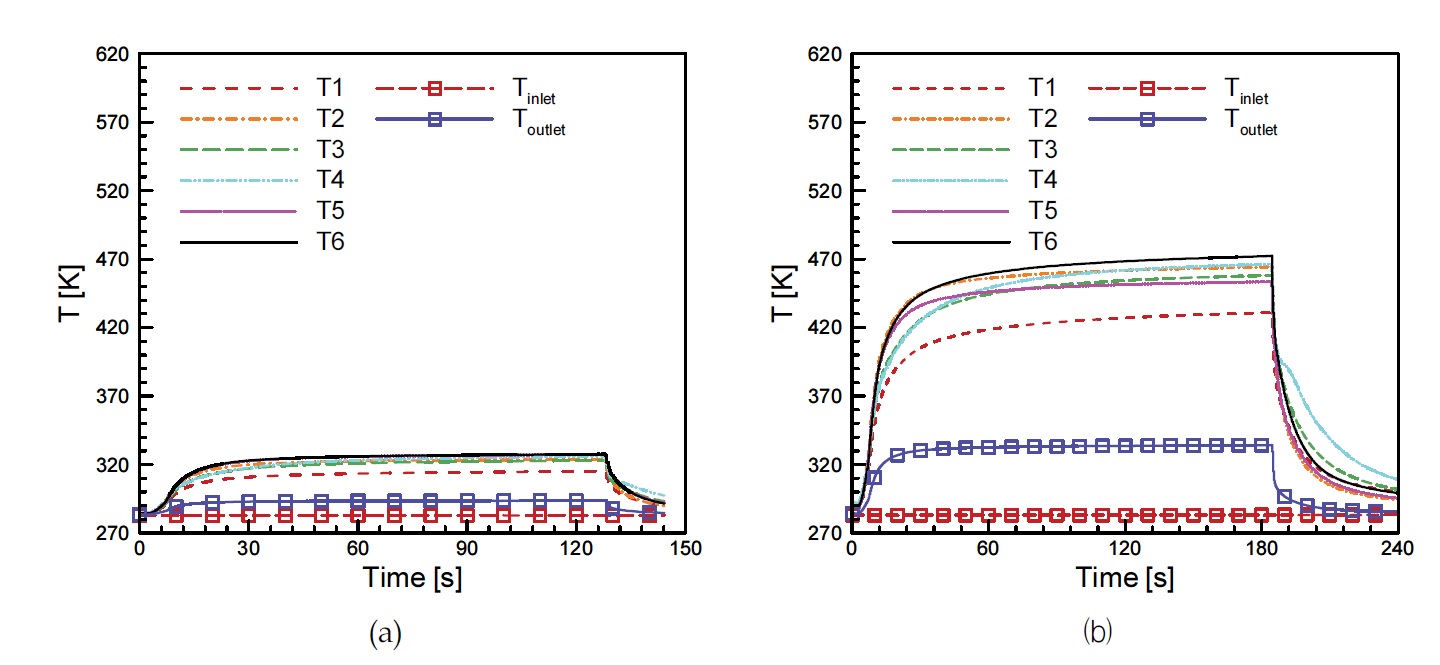
Specimen wall and kerosene temperature distribution with time at di = 2.0 mm, v = 20 m/s, Poutlet = 30 bar, and I = (a) 1500 A and (b) 3000 A.
Fig. 6은 내경 2.0 mm, 후단 압력 50 bar, 인가 전류 2000 A에서 케로신 유속에 따른 결과이다. 유속이 증가하면서 당연히 시편의 벽면 온도(T1∼T6)와 케로신 후단 온도(Toutlet)가 크게 감소하였다. Fig. 6(a)에서 T6 온도가 이론적인 경향성과 맞지 않음을 확인할 수 있다. 모든 시편에서 Re수가 15000 이상인 유속 20 m/s인 경우에는 이런 현상이 없었는데, 유속 10 m/s에서만 T6 온도가 T5보다 낮게 측정되었다. 시편의 길이 방향으로 케로신의 온도가 올라가면서 점성계수는 낮아지고 유동의 Re수는 증가하게 된다. 이러한 이유로 T5와 T6 온도센서 사이에서 유동이 부분 천이에서 완전 난류로 변화하면서, 향상된 냉각성능으로 T6의 온도가 낮아진 것으로 생각된다. 이러한 현상은 RP-3 케로신을 사용한 Wang과 Pan[18]의 실험에서도 관찰되었다.
4.2 대류 열전달계수
열전달 성능을 판단할 수 있는 대표적 값 중 하나가 대류 열전달계수(hl,b)이며, 이 계수가 클수록 Jet A-1이 받는 단위면적당 열전달량이 많다는 것을 의미한다. 앞서 언급했듯 열전달 계산을 위해 정상상태에 근접한 온도 데이터를 사용하고자 시험 가열종료 몇 초 전 동안의 데이터를 평균하여 사용하였다.
Fig. 7은 시편 후단 압력, 유속, 내경을 변수로 구리 벽면 평균온도(Tavg)에 따른 대류 열전달계수를 나타낸 그림이다. 케로신 압력이 임계압력 보다 높은 본 실험에서는 시편 후단 압력이 대류 열전달계수에 거의 영향을 주지 않는다는 것을 다시 확인할 수 있었다. 평균온도가 높아짐에 따라 대류 열전달계수는 약간씩 증가하는 경향성을 나타내었는데, 특히 내경 1.6 mm, 유속 20 m/s에서는 최대 6 kW/m2K까지 상승하였다. 동일 내경, 벽면 평균온도 조건에서 유속이 10 m/s에서 20 m/s로 커지게 되면, 대류 열전달계수도 거의 2배 상승하는 것을 알 수 있다. 이는 Eq. 1과 Eq. 4를 통해 열전달계수는 유속(유량)에 비례하는 것으로부터 예상할 수 있다.
4.3 Nu수 결과 및 Nu수 경험식
Fig. 8은 시편 후단 압력, 유속, 내경을 변화시켰을 때 포용 온도의 함수로 측정된 Nu수를 나타낸 것이다. 포용 온도를 기준으로 한 이유는 Nu수(Nuexp)를 계산하기 위해 포용 온도에서의 Jet A-1 물성을 이용하였기 때문이다. 대류 열전달계수와 마찬가지로 시편 후단 압력은 Nu수 변화에 거의 영향이 없음을 알 수 있다. Nu수는 대류 열전달계수에 비례하기 때문에 Fig. 7과 유사한 경향성을 보인다. 하지만 Eq. 7로부터 예상할 수 있듯이 내경이 커짐에 따라 Nu수는 증가함을 알 수 있다.
Nu수 경험식은 일반적으로 Re수와 Pr수의 함수로 표현된다. Fig. 9(a)에 실험에서 얻어진 Re수에 따른 Nuexp,avg수(Poutlet 30 bar, 50 bar 데이터의 평균값)를 나타내었다. Fig. 9(b)에서는 Pr수의 영향에 대해 비교하고자 하였으며, Pr0.4는 Liang 등[4], Seider 등[19], Dittus 등[20]과 같은 강제대류 열전달 선행 연구자들이 사용해온 수식에 포함된 변수이다. Nuexp,avg/Pr0.4는 거의 일정하게 증가하는 경향성을 보여주지만, Nuexp,avg는 Re수에 따라 선형 관계에서 벗어나는 데이터가 간혹 나타나고 있다. 시편 벽면 온도가 낮은 경우 이러한 현상이 두드러진데, 이는 온도가 낮을 때 물질의 열 확산성을 나타내는 Pr수가 유체의 흐름을 나타내는 Re수 보다 큰 영향력을 가진다고 해석할 수 있다.
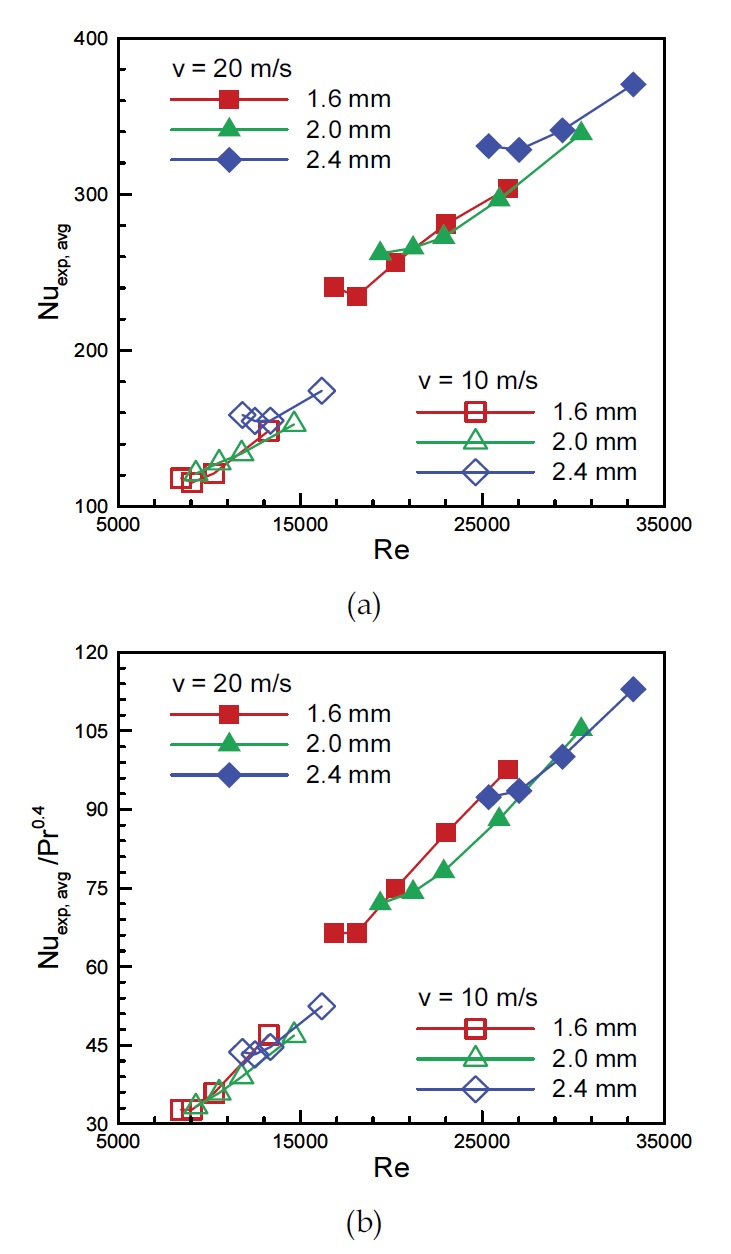
Variation of experimental Nusselt number with Reynolds number. (a) Nuexp,avg and (b) Nuexp,avg/Pr0.4.
Fig. 10에 본 실험에서 측정한 Nu수(Nuexp)를 기존 Nu수 경험식을 통해 계산한 Nu수(Nuref)들과 비교하였다. 사용된 선행 연구들의 Nu수 경험식들은 Eq. 10∼Eq. 13과 같다. Eq. 12에서 µ는 Tb, µw는 Tw.i의 평균값으로 얻어지는 값이며, Eq. 13을 본 실험에 적용 시 Tw는 Tw.i [K], T는 Tb [K], χ는 L, D는 di를 사용하였다. 본 실험결과는 선행 경험식들과 다소 차이를 보이지만 경향성은 유사하였다. 구체적으로 평균 오차는 Eq. 10과 12.76%, Eq. 11과 7.55%, Eq. 12와 5.44%, Eq. 13과 6.34%를 나타내어, Eqs. 12, 13과 유사성이 큰 것을 확인하였다. 이는 Eqs. 12, 13이 다른 식들에 비해 열교환 환경으로부터 측정된 물성을 더욱 고려했기 때문으로 생각된다.
Liang’s et al. equation :
(10) |
Dittus-Boelter’s equation :
(11) |
Sieder-Tate’s equation :
(12) |
Modified Taylor’s equation :
(13) |
위와 같은 선행 경험식들에 근거하여 본 실험 데이터에 적합한 새로운 Nu수 경험식(Eqs. 14∼16)을 도출하였으며, Fig. 11에 실험 데이터와 비교하였다. Nucal는 Eqs. 14∼16를 통해 계산된 값이며, 기존의 선행 경험식들[4,19-22]과 비교하였을 때 상수와 지수에서 다소 차이가 발생하였다. Fig. 11에서 r2는 경험식의 결정계수(coefficient of determination)를 의미하며, 새로운 경험식들은 본 실험 데이터를 매우 정확히 대변한다는 것을 알 수 있다. 본 실험 데이터에 근거할 때 새로 제안한 Eqs. 14∼16은 Pr수가 16∼27 그리고 Re수가 8200∼33400인 Jet A-1 유동에 정확한 식이라 할 수 있다.
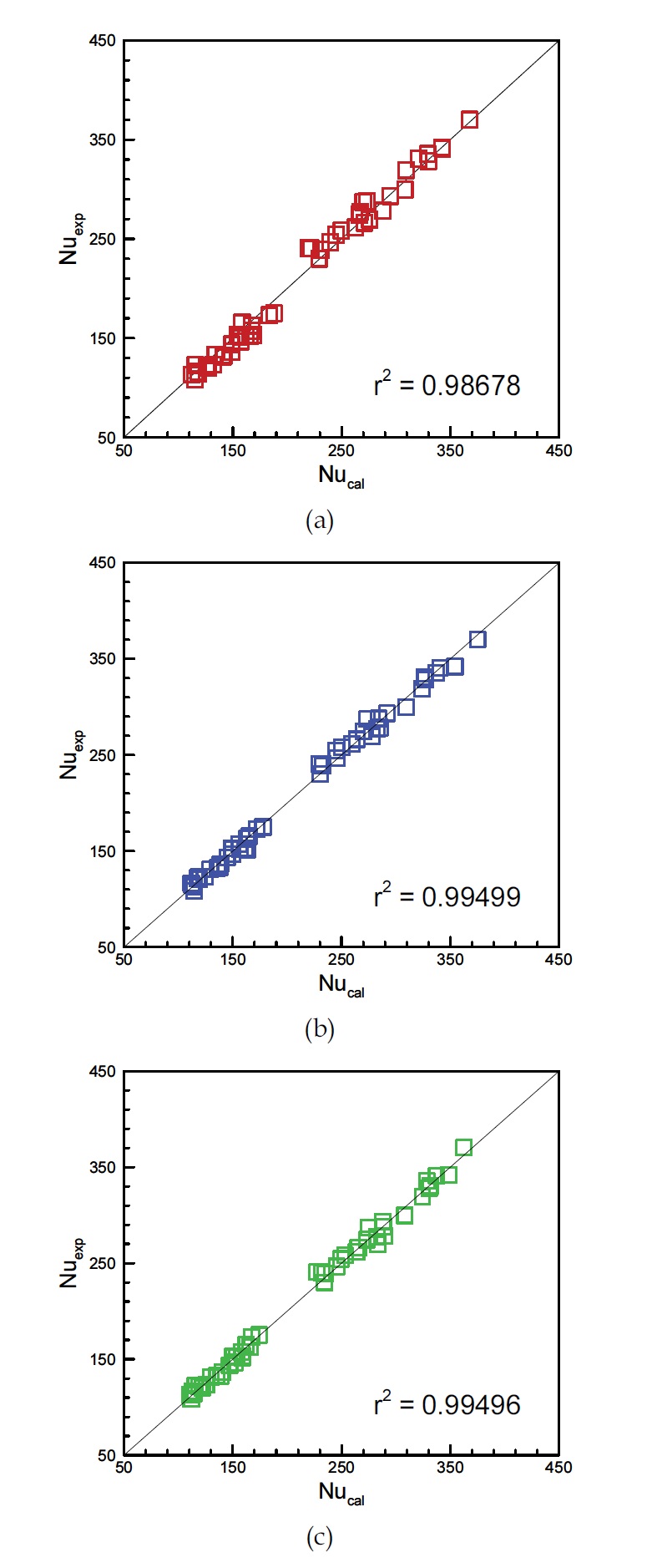
Comparison of experimental Nusselt number (Nuexp) and novel Nusselt number (Nucal) calculated (a) from Eq. 14, (b) from Eq. 15, (c) from Eq. 16.
(14) |
with T [K] for Jet A-1 in circular tubes
(15) |
with T [˚C] for Jet A-1 in circular tubes
(16) |
for Jet A-1 in circular tubes
5. 결 론
전기적 가열방식 모사 재생냉각채널 시편을 이용하여 Jet A-1 케로신의 열전달 특성을 연구하였다. 인가 전류, 모사 시편 지름, 시편 후단 압력, Jet A-1 유속을 변화시키며 시편에서의 벽면 온도 및 시편 전/후단에서의 Jet A-1 온도를 측정하여, 높은 열유속 조건에서 Jet A-1의 대류 열전달계수, Nu수 실험 데이터를 확보하였으며 최종적으로 새로운 Nu수 경험식들을 제안하였다.
일반적으로 대류 열전달계수와 Nu수는 국부적인 위치와 시간에서의 값을 기준으로 측정하게 된다. 본 연구에서는 시편의 길이가 짧고 제작성의 문제 때문에, 길이 방향으로 평균된 대류 열전달계수와 Nu수를 사용하였다. 이러한 문제에도 불구하고 기존의 선행 경험식들과 본 실험결과의 차이는 그리 크지 않았다.
초임계 압력 조건에서 수행된 국내 Jet A-1의 열전달 실험 데이터는 찾기가 어렵다. Jet A-1은 성분의 폭이 넓기 때문에 국내 Jet A-1을 대상으로 얻어진 Nu수 경험식은 한국형발사체 재생냉각 연소기 개발에 좋은 기초자료로 활용될 수 있을 것으로 판단된다.
Nomenclature
A : | Heat transfer area |
CP : | Constant pressure specific heat |
di : | Inner diameter of a specimen |
do : | Outer diameter of a specimen |
h : | Convective heat transfer coefficient |
hl,b : | Convective heat transfer coefficient at the bulk temperature |
I : | Current applied to a specimen |
L : | Length of a specimen |
: | Mass flow rate |
Nu : | Nusselt number |
Nuexp : | Experimental nusselt number |
Pb : | Kerosene bulk pressure |
Poutlet : | Static pressure at the specimen outlet |
Pr : | Prandtl number |
: | Heat flux |
: | Conduction heat flux |
: | Convection heat flux |
Re : | Reynolds number |
tcu : | Copper tube thickness |
Tavg : | Average value of the outside copper temperatures((T1+T2+T3+T4+T5+T6)/6) |
Tb : | Kerosene bulk temperature |
Tinlet : | Kerosene inlet temperature |
Toutlet : | Kerosene outlet temperature |
Tw,i : | Liquid-side copper wall temperature |
Tw,o : | Outside copper wall temperature |
v : | Flow velocity |
V : | Voltage applied to a specimen |
µ : | Dynamic viscosity |
kcu : | Thermal conductivity of the copper at the average outside wall temperature |
kl,b : | Thermal conductivity of kerosene at the bulk temperature |
ρ : | Density |
Acknowledgments
본 논문은 과학기술정보통신부의 재원으로 한국연구재단의 지원(NRF-2013R1A5A1073861, NRF-2018M1A3A3A02065683, NRF-2019M1A3A1A02076962)을 받아서 수행되었으며, 이에 감사드립니다.
References
- Huzel, D.K. and Huang, D.H., Modern Engineering for Design of Liquid-Propellant Rocket Engines, 2nd ed., AIAA, Washington D.C., U.S.A., 1992.
-
Yoon, W., Ahn, K. and Kim, H., “An Experimental Study on Pressure Loss in Straight Cooling Channels, “Journal of the Korean Society of Propulsion Engineers, Vol. 20, No. 4, pp. 94-103, 2016.
[https://doi.org/10.6108/KSPE.2016.20.4.094]
-
Green, J.M., Pease, G.M. and Meyer, M.L., “A Heated Tube Facility for Rocket Coolant Channel Research, “NASA TM-106968, 1995.
[https://doi.org/10.2514/6.1995-2936]
-
Liang, K., Yang, B. and Zhang, Z., “Investigation of Heat Transfer and Coking Characteristics of Hydrocarbon Fuels, “Journal of Propulsion and Power, Vol. 14, No. 5, pp. 789-796, 1998.
[https://doi.org/10.2514/2.5342]
-
Zhong, F., Fan, X., Yu, G. and Li, J., “Heat Transfer of Aviation Kerosene at Supercritical Conditions, “Journal of Thermophysics and Heat Transfer, Vol. 23, No. 3, 2009.
[https://doi.org/10.2514/1.41619]
-
Wang, H., Luo, Y., Gu, H., Li, H., Chen, T., Chen, J. and Wu, H., “Experimental Investigation on Heat Transfer and Pressure Drop of Kerosene at Supercritical Pressure in Square and Circular Tube with Artificial Roughness, “Experimental Thermal and Fluid Science, Vol. 42, pp. 16-24, 2012.
[https://doi.org/10.1016/j.expthermflusci.2012.03.009]
-
Linne, D.L., Meyer, M.L., Edwards, T. and Eitman, D.A., “Evaluation of Heat Transfer and Thermal Stability of Supercritical JP-7 Fuel, “NASA TM-107485, 1997.
[https://doi.org/10.2514/6.1997-3041]
- Park, H.H., Lee, Y.S. and Kim, S.J., “Experimental Investigation on Forced Convective Heat Transfer Characteristic Generated to Heated Tube, “Journal of the Korean Society of Propulsion Engineers, Vol. 10, No. 3, pp. 90-98, 2006.
- Lim, B.J., Lee, K.J., Kim, J.G., Yang, S.H., Kim, H.T., Kang, D.H., Kim, H.J., Han, Y.M. and Choi, H.S., “Hydrocarbon Fuel Heating Experiments Simulating Regeneratively Cooled Channels of LRE Combustor, “Journal of the Korean Society of Propulsion Engineers, Vol. 11, No. 5, pp. 78-84, 2007.
- Jeon, T.J. and Park, T.S., “Three-dimensional Turbulent Heat Transfer in a Liquid Rocket Engine with Regenerative Cooling Passages, “46th KSPE Spring Conference, Jeju, Korea, pp. 142-147, May 2016.
- Park, T.S., “Development of a Thermal Analysis Program for a Regenerative Cooling Passage of Liquid Rocket and Simulation of Turbulent Heat Transfer, “Journal of Computational Fluids Engineering, Vol. 8, No. 3, pp. 56-65, 2003.
- Seo, H.W., “A Numerical Simulation of Regenerative Cooling Heat Transfer Process for the Liquid Propellant Rocket Engine, “Journal of the Korean Society of Propulsion Engineers, Vol. 2, No. 3, pp. 54-61, 1998.
- Lemmon, E.W., Huber, M.L. and McLinden, M.O., “NIST Reference Fluid Thermodynamic and Transport Properties—REFPROP V9.1, “NIST, Gaithersburg, M.D., U.S.A., Apr. 2013.
-
Pei, X., Hou, L. and Ren, Z., “Kinetic Modeling of Thermal Oxidation and Coking Deposition in Aviation Fuel,” Energy & Fuels, Vol. 31, No. 2, pp. 1399-1405, 2017.
[https://doi.org/10.1021/acs.energyfuels.6b02869]
-
Liu, Z., Bi, Q., Guo, Y., Yan, J. and Yang, Z., “Convective Heat Transfer and Pressure Drop Characteristics of Near-Critical-Pressure Hydrocarbon Fuel in a Minichannel,” Applied thermal engineering, Vol. 51, No. 1-2, pp. 1047-1054, 2013.
[https://doi.org/10.1016/j.applthermaleng.2012.10.029]
-
“Igor Pioro and Sarah Mokry (January 28th 2011) Heat Transfer to Supercritical Fluids, “retrieved 17 Jan. 2020 from https://www.intechopen.com/books/heat-transfer-theoretical-analysis-experimental-investigations-and-industrial-systems/heat-transfer-to-supercritical-fluids, .
[https://doi.org/10.5772/13792]
-
Edwards, T. and Zabarnick, S., “Supercritical Fuel Deposition Mechanisms,” Industrial & engineering chemistry research, Vol. 32, No. 12, pp. 3117-3122, 1993.
[https://doi.org/10.1021/ie00024a022]
-
Wang, N. and Pan, Y., “Correlation for Heat Transfer of RP-3 Kerosene Flowing in Miniature Tube at Supercritical Pressures, “Modern Physics Letters B, Vol. 34, No. 12, pp. 2050116, 2020.
[https://doi.org/10.1142/S021798492050116X]
-
Sieder, E.N. and Tate, G.E., “Heat Transfer and Pressure Drop of Liquids in Tubes, “Industrial and Engineering Chemistry, Vol. 28, No. 12, pp. 1429-1435, 1936.
[https://doi.org/10.1021/ie50324a027]
-
Dittus, F.W. and Boelter, L.M.K., “Heat Transfer in Automobile Radiators of the Tubular Type, “International Communications in Heat and Mass Transfer, Vol. 12, pp. 3-22, 1985.
[https://doi.org/10.1016/0735-1933(85)90003-X]
- Welty, J.R., Wicks, C.E., Wilson, R.E. and Rorrer, G.L, Fundamentals of Momentum, Heat, and Mass Transfer, 5th ed., John Wiley & Sons Inc., New Jersey, N.J., U.S.A., 2007.
-
Winterton, R.H.S., “Where did the Dittus and Boelter equation come from?, “International Journal of Heat and Mass Transfer, Vol. 41, No. 4, pp. 809-810, 1998.
[https://doi.org/10.1016/S0017-9310(97)00177-4]