
탈규소화를 통한 LSI-Cf/SiC 복합재료의 내산화성 향상
Copyright Ⓒ The Korean Society of Propulsion Engineers
This is an Open-Access article distributed under the terms of the Creative Commons Attribution Non-Commercial License(http://creativecommons.org/licenses/by-nc/3.0) which permits unrestricted non-commercial use, distribution, and reproduction in any medium, provided the original work is properly cited.
초록
Cf/SiC 복합재는 저밀도, 높은 기계적 강도, 우수한 열 안정성을 가지고 있어 로켓 추진기관, 항공 및 군사 분야 등의 고온 응용 산업에 유망한 재료이다. 그러나 용융 실리콘 함침(Liquid Silicon Infiltration, LSI) 공정을 통해 제작된 복합재는 잔존하는 Si에 의하여 물리적, 열적 특성이 저하된다. 본 논문에서는 LSI 공정을 통해 제작된 Cf/SiC 복합재의 내부 Si을 제거하기 위한 방안으로 탈규소화(de-siliconization) 공정을 도입하였다. 최대 5분 동안 옥시아세틸렌 토치 테스트를 진행하고 시편의 산화된 표면과 단면은 3D scanning, X-ray diffraction(XRD), 광학현미경(OM), 전자주사현미경(SEM)으로 분석하였다.
Abstract
Cf/SiC composites have low density, high mechanical strength, and good thermal stability, making them promising materials for high-temperature applications such as rocket propulsion and military fields. However, the remaining Si deteriorates physical and thermal properties. In this paper, the de-siliconization was introduced as a method to remove the Si of the Cf/SiC composite fabricated through Liquid Silicon Infiltration(LSI) process. The stability of composite has been tested under an oxyacetylene torch flame for up to 5 minutes. The oxidized surface and cross section of specimens were characterized by 3D scanning, X-ray diffraction(XRD), Optical microscope(OM) and Scanning electron microscope(SEM).
Keywords:
Cf/SiC Composite, Liquid Silicon Infiltration, De-Siliconization, Oxidation Resistance키워드:
Cf/SiC 복합재, 용융 실리콘 함침, 탈규소화, 산화 저항성1. 서 론
산업이 발달함에 따라 초고온(1200 °C 이상)에서 사용할 수 있는 초고온 구조 재료에 대한 개발이 요구되고 있다[1]. 특히 제트엔진, 로켓의 노즐 부분과 같은 작동온도가 매우 높은 분야에서 초고온 복합재료에 대한 관심이 높아지고 있으며 그 중 탄소 섬유 강화 세라믹 복합재료는 저밀도, 높은 기계적 강도, 높은 비탄성률, 우수한 열 안정성, 뛰어난 산화 및 내마모성을 갖추어 고온 응용분야에서 더욱 유망한 재료이다[2]. 대표적인 복합재료로 Carbon-Carbon composite는 우수한 기계적 강도와 고온 안정성을 가지고 있고 복합재료 구성물질의 조합에 따라서 열안정성 및 기계적 강도와 같은 물리적인 특성을 향상시킬 수 있다[3-5]. 그 중에서도 탄화규소(SiC) 재료는 1400 °C 이상의 고온에서도 견디는 특성, 화학적 안정성이 아주 우수한 세라믹 물질로 주목받고 있다. Cf/SiC 복합재를 구성하게 되면 SiC matrix가 carbon fiber를 외부 파괴요인으로부터 보호하는 기능을 하게 되어 우수한 내산화성을 가지게 된다.
Cf/SiC 복합재는 다양한 방법으로 제작할 수 있다. 예를 들어 Chemical Vapor Infiltration(CVI), Polymer Impregnation and Pyrolysis(PIP), 그리고 Liquid Silicon Infiltration(LSI) 방법 등이 있다. LSI 방법은 낮은 공정가격과 간편한 공정이라는 장점을 가지고 있다[6]. LSI 공정은 2가지의 과정을 거치게 된다. 먼저 탄화 과정(Carbonization process)을 통하여 carbon fiber preform에 미세 크랙을 유도한다. 유도된 크랙은 Si이 infiltration 될 수 있도록 하는 경로가 된다. 다음으로 용융된 Si이 유도되어 있는 통로를 따라서 infiltration 이 진행된다. 이 때 온도는 Si의 녹는점인 1,420 °C를 상회한다. 용융된 Si이 높은 온도에서 함침되고 나서 carbon fiber 와 반응하여 SiC를 형성하게 되고 carbon 섬유의 기공을 채움으로써 복합체의 밀도를 향상시키게 된다[7]. 하지만 LSI 공정은 한계도 분명하다. 복합체 내 잔존 Si이 존재하게 되는데, 이는 고온에서 산화되면서 열적, 기계적 강도를 감소시킨다. 특성 저하의 원인인 Cf/SiC 복합체 내의 잔존 Si을 줄이기 위한 다양한 연구들이 진행되고 있다[8]. Autoclave vacuum bagging 방법을 통해 잔존 Si을 제거하거나 Si-Cr을 함침시켜 CrSi2 형성을 유도하여 굽힘 강도와 인성을 향상시키는 연구가 진행되고 있다[6]. 본 연구에서는 Cf/SiC 복합체에 Ultra High Temperature Ceramics(UHTC)의 한 종류인 ZrB2를 첨가하여 Cf/SiC-ZrB2 복합재를 제작하고 탈규소화 공정을 거친 시편에 대하여 토치테스트를 이용하여 내산화성 및 내삭마성을 비교하고자 한다.
2. 본 론
2.1 Cf/SiC 복합재료
본 연구에서 사용된 탄소섬유 프리프레그는 페놀수지(KRD-HM2, 코오롱 화학)와 함께 평면 탄소직물(CF3327, Hankuk Adv. Mat., South Korea)을 사용하여 제조하였다. ZrB2 분말 (97+%, High purity Chem., Japan)을 페놀수지와 에탄올과 함께 24시간 동안 ball milling 하였다. ZrB2의 첨가량은 혼합 슬러리 중량 기준으로 0 wt%, 30 wt%이며, 이는 각각 시편 Z00와 Z30에 해당한다. 슬러리가 함침 된 탄소섬유를 40-layer로 적층하고 오토클레이브에서 120 °C, 6 bar의 조건에서 경화시켰다. 경화된 시편을 질소 분위기, 600 °C에서 12시간 동안 처리하여 잔류물을 제거하였다. 최종적으로 진공 퍼니스를 이용하여 1600 °C에서 탄화시켜 다공성의 Cf/C 성형체를 제작하였다.
LSI 공정은 질화붕소가 코팅된 흑연 도가니에 Si 분말과 Cf/C 성형체를 넣고 진공 분위기에서 1600 °C로 30분간 가열하여 용융된 Si을 Cf/C 성형체 안으로 함침시키는 방식으로 진행하였다. LSI가 진행된 시편은 옥시아세틸렌 토치 테스트 및 추가분석을 위해 20 mm x 20 mm x 7 mm 의 직육면체로 가공하였다.
Cf/SiC-ZrB2 복합재료의 탈규소화 공정은 진공로에서 1800 °C에서 1시간 동안 진행하였다. Fig. 1과 같이 시편을 흑연 도가니에 넣고 carbon felt로 시편주위를 감싸서 빠져나오는 잔존 Si을 흡수하도록 하였다.
2.2 Oxyacetylene torch test
Cf/SiC-ZrB2 복합재의 내삭마성 및 내산화성은 lab scale의 oxyacetylene 토치를 사용하여 평가하였다. 시편을 흑연 홀더에 고정 시키고 토치 팁으로부터 70 mm 떨어진 곳에 시편 표면이 오도록 설정하였다. 아세틸렌과 산소의 유량은 Mass Flow Controller(MFC, M3030V, Linetech, South Korea)로 조절하였으며, 유량은 각각 10 L/min(C2H2)와 13 L/min (O2)로 설정하였다. 이때의 열 유속은 800 W/cm2로 측정되었다. 모든 시편에 대하여 300초 동안 진행하고 도중의 온도 프로파일 변화는 2색 고온계(Pyrospot DSR 10NV, DIAS Infrared GmbH, Germany)를 이용하여 측정하였다.
2.3 시험장비 및 방법
Cf/SiC-ZrB2 복합재의 결정상은 X선 회절계(XRD, Rigaku, SmartLab, Japan)를 사용하여 확인하였다. 시편의 중앙을 절단하고 단면의 미세구조를 광학현미경(Optical digital microscope, Dino-Lite, Dunwell Tech. U.S.A.)과 전자주사현미경(Scanning electron microscope, SU-5000, Hitachi. Japan)을 이용하여 분석하였다. 3D 스캔을(ATOS 5, GOM GmbH, Germany) 통하여 산화/삭마 시험 후 표면 프로파일과 삭마 깊이를 분석하였다. 복합재료의 굽힘 강도는 만능시험기(Instron 5583, Instron Corporation, USA)를 사용하여 3점 굽힘 시험을 수행하였다. 시편을 직사각형 막대(3 mm x 4 mm x 25 mm)로 가공하고 크로스헤드 속도는 0.5 mm/min으로 설정하여 10개의 시편을 측정 후 평균하여 굽힘강도를 계산하였다. 시편의 밀도는 증류수를 사용한 아르키메데스 방법을 통하여 측정하였다.
3. 결과 및 고찰
본 연구에서는 Cf/SiC-ZrB2 복합재료의 탈규소화 공정시행 여부에 따른 내삭마성 시험평가 후 표면 프로파일, 상 형성, 무게 및 강도 특성변화를 분석하였다.
3.1 탈규소화(De-siliconization) 공정
LSI 공정을 통하여 Cf/SiC 복합재를 제작하고 내부에 존재하는 Si을 제거하기 위하여 오토클레이브 공정과 탈규소화 공정을 수행하였다. 오토클레이브와 탈규소화 공정을 모두 진행하며 잔존 Si을 최대한 제거하였다. 탈규소화 공정을 거친 후, Z00의 샘플은 –10.1%, Z30은 –9.1%의 무게변화를 나타내었다. LSI 공정 이후 잔존하는 free Si 양은 ZrB2 함량에 따라 차이는 있었지만 탈규소화가 정상적으로 진행됨을 알 수 있다. Fig. 2는 탈규소화 공정을 거친 복합체의 X-ray diffraction pattern을 나타낸다.
결정질의 SiC 회절피크를 확인할 수 있으며 또한 탈규소화 공정을 거친 시편에서는 Si의 회절 강도가 크게 감소한 것을 확인할 수 있다. 이를 통해 탈규소화 공정이 효과적으로 진행되었음을 알 수 있다. 한편 탈규소화 공정을 거친 후 시편을 반으로 잘라 단면을 관찰한 이미지를 Fig. 3에 나타내었다. Optical microscope(OM) 이미지를 보면 UHTC 첨가에 관계없이 Si이 빠져나간 자리는 pore channel 로 형성됨을 확인할 수 있다. Z30의 전자주사현미경 이미지인 Fig. 3(f)를 통하여 ZrB2가 복합재 matrix에 분포되어 있는 것을 확인하였다. 하지만, ZrB2 첨가에 따른 pore channel 및 crack path 형성에는 큰 차이가 없었다.
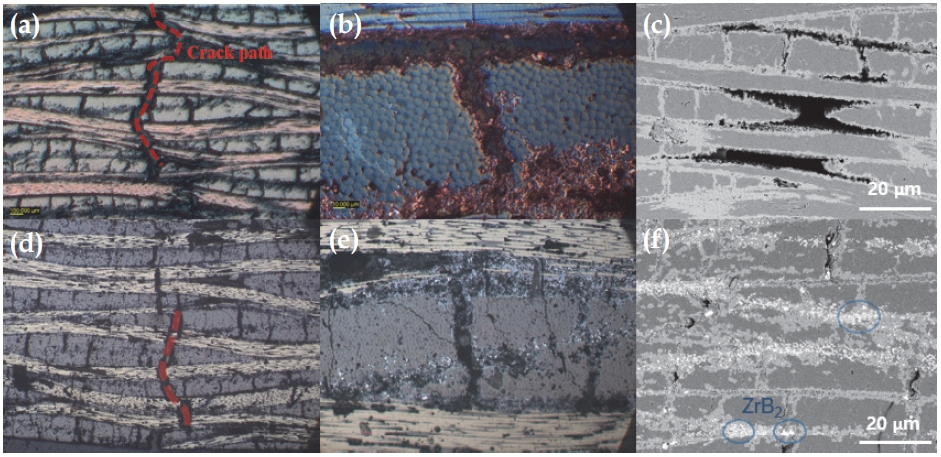
Optical and scanning electron microscope image of Cf/SiC-ZrB2 composite (a), (b) and (C) Z00 (d), (e) and (f) Z30.
Fig. 4는 복합재료의 굽힘강도와 밀도 수치를 나타낸 것이다. 탈규소화를 진행하지 않은 시편의 굽힘강도는 모든 조성에서 120 MPa 이상으로 측정되었다. 한편 탈규소화를 거친 시편은 조성에 따라 80 MPa 미만의 굽힘강도를 나타내었다. 이는 Fig. 3의 OM 이미지 상에서도 관찰했듯이 탈규소화 진행 후, Si이 존재하였던 자리가 pore channel로 남게 되어 crack의 전파 경로를 제공함에 따라 탈규소화 공정을 진행한 시편의 굽힘강도가 감소하는 것으로 판단할 수 있다. 이와 같이 굽힘강도가 감소하는 것은 탈규소화가 내부에 존재하는 Si이 빠져나오고 남은 자리를 pore로 남게 하는 것이 주된 원인으로 작용한다. Si이 빠져나옴으로 기인한 무게변화는 탈규소화 후 밀도변화의 결과로 나타난다. Z00은 1.978 g/cm3에서 1.867 g/cm3로 0.111 g/cm3의 밀도변화를 보였고 Z30은 2.377 g/cm3에서 2.284 g/cm3로 0.093 g/cm3의 변화를 보였다. ZrB2가 나머지 matrix의 공간을 차지하여 잔존하는 free Si의 양을 줄여 무게 변화 및 밀도 변화를 감소시킨 것으로 판단된다. 물리적 특성이 감소되는 이유인 LSI 공정 이후 잔존하는 Si 양을 줄여 pore channel 형성을 감소시키거나 이미 생성된 pore channel에 다른 내열성 물질로 함침시키는 방안이 있을 수 있다.
3.2 Oxyacetylene torch test
LSI 와 탈규소화 공정을 완료한 Cf/SiC-ZrB2 복합재료를 20 mm x 20 mm 크기로 절단하고 300초 동안 옥시아세틸렌 토치 테스트를 진행하여 복합재료의 내산화성 및 표면 내삭마성을 비교하였다. 탈규소화를 진행한 Z00, Z30 시편 모두 옥시아세틸렌 토치 테스트를 진행하면 고온 산화분위기에 노출되고 탈규소화 공정 진행 후 형성되는 경로를 따라서 산소의 유입이 더욱더 활발하게 일어나게 된다. 이러한 경로는 옥시아세틸렌 토치 테스트 이후 시편의 무게가 감소하는 주된 요인으로 작용하여 내부의 탄소섬유가 산소와 반응하여 CO2로 날아가는 현상이 일어나게 된다.
옥시아세틸렌 토치 시험 이후 표면상태와 3D 스캐닝 결과로부터 Z00, Z30의 표면상태와 산화정도는 크게 다름을 알 수 있다. Fig. 5와 Fig. 7은 각각 Z00, Z30의 탈규소화 공정 여부에 따른 토치 테스트 이후 표면상태와 3D 스캐닝 프로파일 이미지이다. Fig. 5(a)에서 보이듯이 표면에 하얗게 산화층이 발달된 것을 확인할 수 있다. 이는 내부에 잔존해 있던 Si이 표면에서 산화되면서 SiO2가 표면을 뒤덮은 것으로 판단된다. 3D 스캐닝에서도 표면상의 SiO2 형성으로 인하여 depth가 오히려 증가한 것을 확인할 수 있다. 이와 다르게 탈규소화 공정을 거쳐 잔존해 있는 Si의 양을 줄인 시편의 경우, 토치 테스트 시험 중 표면으로 용출되는 Si의 양이 현저히 감소되어 표면상태도 깨끗한 것을 확인하였다. 다만, 탈규소화 공정을 거친 시편의 표면에서도 pore channel이 형성이 되어 표면 거칠기(roughness) 가 소폭 증가하게 된다. 거칠기가 증가함에 따라 토치 산화 반응에 대한 표면적이 늘어나게 되고 일부 삭마가 일어남을 Fig. 5(d)에서 확인할 수 있다. Fig. 6, 8은 각각 Z00, Z30의 탈규소화 공정 여부에 따른 토치 테스트 이후 시편의 X-ray diffraction pattern을 나타낸 것이다. 먼저 탈규소화를 진행하지 않은 Z00 시편은 토치 테스트 이후, 표면에 두꺼운 무정질의 SiO2 층이 생성되어 X-ray diffraction pattern에서도 회절피크가 broad 하게 나타났다. 하지만 탈규소화를 진행한 시편에서는 SiC의 결정질 회절 피크를 확연히 확인할 수 있으며 이는 표면 내산화성이 크게 향상된 것을 의미한다. Z30은 토치 테스트 전후로 큰 변화는 없었지만 2-theta 30° 미만에서 monoclinic의 ZrO2 phase를 확인하였으며 일부 잔존 Si 이 표면에서 관찰되었다. Z30은 고온 산화분위기에서 표면에 ZrO2를 형성하고 내삭마성이 향상됨을 Fig. 7(c), (d)에서 확인할 수 있다. ZrB2가 첨가되어 내산화성과 내삭마성이 개선된 이유로는 표면에 ZrO2 산화층이 형성되고 이 산화층이 시편 내부로의 산소의 확산을 차단하여 추가적인 산화와 삭마를 막는 역할을 하기 때문이다.
탈규소화를 진행한 Z00 및 Z30은 X-ray diffraction pattern에서도 Si 회절피크가 나타나지 않거나 크게 감소하였고 토치 테스트 이후 표면상태가 우수하였다. 이를 통해 탈규소화 과정이 복합재 내의 잔존 Si을 줄여 내산화성 향상에 영향을 주었음을 확인하였다.
4. 결 론
Cf/SiC 복합재료에 대한 LSI, 탈규소화 공정에 따른 torch test 전후의 내산화성 특성을 연구하였다. 실험결과로부터 얻은 결론은 다음과 같다.
탈규소화 공정을 적용한 시편은 빠져나온 Si에 따라서 내부에 pore channel이 형성됨을 확인하였고 이는 굽힘강도 감소의 결과로 나타났다. 하지만, 토치 테스트 이후 표면상태는 탈규소화를 진행한 시편이 우수한 것을 확인하였다. ZrB2를 첨가한 Cf/SiC-ZrB2 복합재는 전체적인 표면 내산화성이 증가하였지만 탈규소화를 진행하지 않은 시편에서는 ZrB2를 첨가하지 않은 시편과 동일하게 표면에서 용출된 Si에 의한 반응이 관찰되었다. 탈규소화를 진행한 시편은 토치 테스트 이후에도 개선된 표면 상태를 보였으며 이를 통하여 복합재의 탈규소화 공정이 표면상태, 내산화성 개선방법으로 제시될 수 있음을 확인하였다.
Acknowledgments
본 연구는 정부(과학기술정보통신부)의 재원으로 한국연구재단 – 스페이스챌린지사업(NRF-2021M1A3B8078916) 및 방위사업청과 국방과학연구소의 국방 고기동 상층추진기술 특화연구실에서 수행된 사업(UD210022SD)의 지원을 받아 수행된 연구이며 이에 감사드립니다.
References
-
G.W. Meetham, “High-temperature materials — a general review,” Journal of Materials Science, Vol. 26, pp. 853-860, 1991.
[https://doi.org/10.1007/BF00576759]
-
W. Tsung-Ming, W. Wen-Cheng, H. and Shu-En, “Temperature dependence of the oxidation resistance of SiC coated carbon/carbon composite,” Materials Chemistry and Physics, Vol. 33, pp. 208-213, 1993.
[https://doi.org/10.1016/0254-0584(93)90064-S]
-
S. Beyer, F. Strobel and H. Knabe, “Development and Testing of C/SiC Components for Liquid Rocket Propulsion Applications,” 35th Joint Propulsion Conference and Exhibit, Los Angeles, U.S.A., AIAA-99-2896, June 1999.
[https://doi.org/10.2514/6.1999-2896]
-
Y.-C. Zhu, S. Ohtani, Y. Sato and N. Iwamoto, “The improvement in oxidation resistance of CVD-SiC coated C/C composites by silicon infiltration pretreatment,” Carbon, Vol. 36, No. 7-8, pp. 929-935, 1998.
[https://doi.org/10.1016/S0008-6223(97)00207-8]
-
Kong, J.H., Baek, C., Yun, J.H., Lim, S.T., Kim, J.-H. and Kim, D.K., “Enhanced thermal stability of W-25Re/Ti/carbon-carbon composites via gradient diffusion-bonding,” Journal of Alloys and Compounds, Vol. 924, 166549, 2022.
[https://doi.org/10.1016/j.jallcom.2022.166549]
-
Kim, S., Han, I.S., Seong, Y.-H. and Kim, D.K., “Mechanical properties of C–SiC composite materials fabricated by the Si–Cr alloy melt-infiltration method,” Journal of Composite Materials, Vol. 49, No. 24, pp. 3057-3066, 2015.
[https://doi.org/10.1177/0021998314559279]
- W. Braue, R. Pleger and R. Weiss, “The nanoscale microstructure of 2D C/C-SiC ceramic composites processed via silicon capillary impregnation,” International Conference on High Temperature Ceramic Matrix Composites, Santa Barbara, U.S.A., 134935, Aug. 1995.
-
P. Tao, K. Li and Y. Wang, “Effects of preform structure on microstructure and mechanical properties of C/SiC composites reinforced by Si3N4 nanowires,” Ceramics International, Vol. 44, No. 5, pp. 5719-5725, 2018.
[https://doi.org/10.1016/j.ceramint.2017.12.225]