
금속선이 삽입된 추진제 그레인의 Burn-back 해석
Copyright Ⓒ The Korean Society of Propulsion Engineers
This is an Open-Access article distributed under the terms of the Creative Commons Attribution Non-Commercial License(http://creativecommons.org/licenses/by-nc/3.0) which permits unrestricted non-commercial use, distribution, and reproduction in any medium, provided the original work is properly cited.
초록
금속선이 삽입된 추진제 그레인은 높은 충전율을 유지하면서 연소속도를 증가시키기 위해 사용되어왔다. 금속선이 삽입된 추진제 그레인을 사용하는 추진기관의 성능설계를 위해서는 금속선의 위치, 개수, 배치각도, 금속선에서의 추진제 연소속도 증가비에 따른 burn-back 해석이 요구된다. 본 연구에서는 금속선이 삽입된 추진제 그레인의 설계변경에 대응하여 신속하게 연소면적을 계산할 수 있는 수치적 방법이 개발되었다. 개발된 방법과 CAD 프로그램으로부터 도출된 연소면적 결과를 비교하였으며, 격자의 반경방향 크기가 줄어들수록 오차율이 줄어드는 것을 확인 했다. 금속선의 개수 및 위치변경에 따른 영향성 분석이 수행되었으며, 금속선의 개수가 증가하면 연소초기 및 말기 구간이 짧아지고 정상상태구간이 길어지는 것이 확인되었다. 금속선을 배치할 때, 서로 다른 반경에 금속선을 배치하는 경우에서 동일한 반경에 금속선을 배치하는 경우보다 연소초기 영역에서의 연소면적이 급증하고 연소말기에서 연소면적이 급감하는 것이 확인되었다.
Abstract
Propellant grains with embedded metal wires have been used for enhancement of burning rate while maintaining high loading density. For the performance design of a solid rocket motor using propellant grain with embedded metal wires, burn-back analysis is required according to number, location, arrangement angle of metal wires, and augmentation ratio of the propellant burning rate near a wire region. In this study, a numerical method to quickly calculate a burning surface area was developed in response to the design change of the propellant grain with embedded metal wires. The burning surface area derived from the developed method was compared with the results of a CAD program. Error rate decreased as the radial size of the grid decreased. Analysis for characteristics of burning surface area was performed according to the number and location of metal wires, the initial and final phases were shortened and the steady-state phase was increased when the number of metal wires increased. When arranging the metal wires at different radii, the burning surface area rapidly increased in the initial phase and sharply decreased in the final phase compared to the case where the metal wires were disposed in the same radius.
Keywords:
Solid Rocket Motor, Enhanced Burning Rate, Propellant Grain with Embedded Metal Wire, Burn-back Analysis키워드:
고체추진기관, 연소속도증가, 금속선이 삽입된 추진제 그레인, Burn-back 해석1. 서 론
고체 추진기관의 추력성능은 연소과정 중 변화되는 추진제 그레인의 연소면적에 지배적인 영향을 받으며, 추진제 그레인은 요구추력성능에 따라 다양한 형상으로 설계된다.
추진제 그레인은 연소형상에 따라 끝단연소 그레인(end-burning grain)과 내면연소 그레인(perforated grain)으로 구분 될 수 있다. 전자의 경우 추진제 충전율이 높고 구조적 안전성이 우수한 장점을 가지고 있지만, 원통형인 추진제 그레인의 길이방향에 위치한 한쪽 면만이 연소되기 때문에, 연소면적변화가 적고 추력수준을 증가시키는 설계가 어렵다. 후자의 경우 연소면적변화에 대한 설계가 비교적 자유롭고 추력수준을 증가시키는 설계가 용이하지만 추진제 충전율 및 구조안전성이 떨어질 수 있다.
끝단연소의 장점을 유지하면서 연소면적변화설계가 가능한 방법으로 추진제 그레인에 금속선을 삽입하는 기술이 사용되어 왔다. 금속선이 삽입된 추진제 그레인의 연소형상은 열전달이 높은 금속선의 영역에서 추진제 영역보다 연소속도가 빠르기 때문에 금속선을 중심으로 하는 원뿔모양의 형태로 나타나며 연소면적증가를 발생시킨다[1].
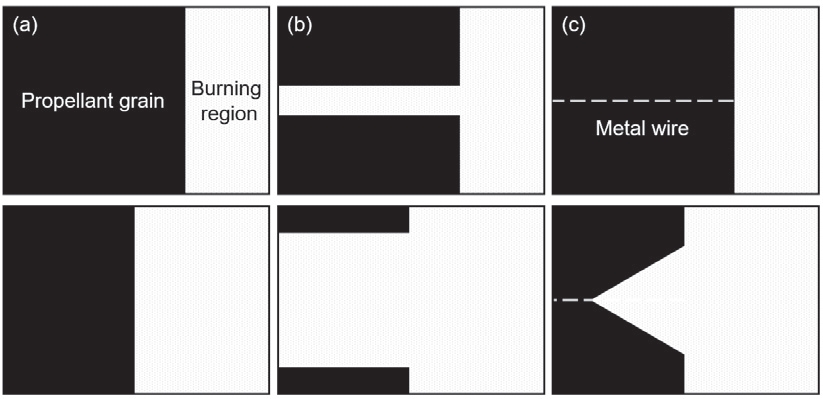
Schematic diagrams for burning process of solid propellant grains (a: end-burning grain, b: perforated grain, c: grain with embedded a metal wire).
금속선이 삽입된 추진제 그레인은 금속선의 종류에 따라 연소면적변화설계를 다양화 할 수 있고 원하는 추진제 그레인 부분에만 금속선을 삽입하면 다양한 추력선도를 제공할 수 있어 관측로켓, 전술탄도유도탄 등에 적용되어 왔다[2].
금속선이 삽입된 추진제 그레인과 관련된 연구들을 살펴보면, 초기에는 추진제와 금속선 사이의 열전달을 이론적으로 모델링하거나 추진제와 금속선의 물리적 성질들로 도출된 실험식을 사용하여 연소속도 증가비를 예측하는 연구[3-7]와 금속선의 굵기, 종류, 추진제와 금속선사이에 첨가되는 접착제 등에 따른 연소속도 증가특성에 대한 연구[8-10]가 수행되었다. 최근에는 높은 온도에서 발열반응을 수반하는 금속선을 사용하거나 마이크로파가열을 적용하는 등 금속선으로부터 추진제로의 열전달을 증폭시켜 능동적으로 연소속도 증가비를 증가시키는 연구가 수행되었다[11-14].
한편 금속선이 삽입된 추진제 그레인의 연소형상을 예측하고 연소표면적을 계산하는 burn-back 해석과 관련된 연구는 찾아보기 어렵다. 그러나 금속선이 삽입된 추진제 그레인을 사용하는 추진기관의 추력성능설계를 위해서는 금속선의 위치, 개수, 배치각도, 금속선에서 추진제의 연소속도 증가비 등 설계변수 변경에 따른 burn-back 해석이 필요하다.
추진제 그레인의 burn-back 해석방법으로 해석적 방법, CAD(Computer Aided Design) 프로그램을 사용하는 방법, 수치적 방법이 있다. 해석적 방법은 추진제 그레인의 연소되는 형상을 기하학적으로 분석하고 연소면적에 대한 관계식을 도출하는 것으로 기하학적 해석이 어려운 경우 적용하기 힘들고 설계변수 변경에 따라 새로운 관계식을 도출해야하는 번거로움이 있다. CAD 프로그램을 사용하는 방법은 추진제 그레인이 연소되는 형상을 CAD 프로그램 사용자가 기하학적으로 예측하여 작도하고 연소면을 지정하여 면적정보를 얻어내는 방법이다. 해당방법은 추진제 그레인의 연소면 후퇴진행에 따라 그레인의 형상을 반복적으로 작도해야하므로 많은 작업시간을 필요로 한다. 최근에는 API(Application Programming Interface) 기능과 매크로를 제공하는 CAD 프로그램을 활용하여 연소면 정보획득을 자동화하는 방법이 소개되기도 했다. 수치적 방법은 추진제 그레인 연소면의 거동을 미분방정식의 형태로 표현하고 수치해석을 수행하는 것으로 다양한 추진제 그레인 형상에 범용으로 사용될 수 있으나 수치적 오차를 동반하고 많은 계산비용이 소요될 수 있다[15,16].
본 연구에서는 금속선이 삽입된 추진제 그레인의 설계변수 변경에 대응하여 신속하게 그레인의 연소면을 예측하고 연소면적을 계산하는 수치기법이 개발되었다. 해당기법은 금속선이 삽입된 추진제 그레인의 연소초기부터 말기까지의 연소면적변화를 큰 계산비용 없이 신속하게 도출 할 수 있다는 장점이 있다. 개발된 계산방법의 유효성 검증을 위하여, CAD 프로그램과 개발된 방법을 통해 도출된 연소면적결과를 비교하였으며, 추가로 금속선의 개수 및 위치변경에 따른 영향성 분석이 수행되었다.
2. 금속선이 삽입된 추진제 그레인
2.1 금속선이 삽입된 추진제 그레인의 Burn-back
Fig. 2에서 금속선이 삽입된 추진제 그레인의 burn-back 과정을 나타냈다. 금속선에서 추진제의 연소속도(rw)는 금속선이 없는 영역에서의 추진제 연소속도(r)보다 빠르게 나타나는데, 금속선에서의 열전달을 능동적으로 제어하지 않는 경우 연소종료까지 연소속도 증가비(α = rw/r)는 일정하게 유지된다. 연소속도 증가비는 금속선이 삽입된 추진제 그레인의 burn-back에서 발생되는 원뿔의 반각(θ)과 사인함수의 관계(sin(θ) = 1/α)로 나타난다.
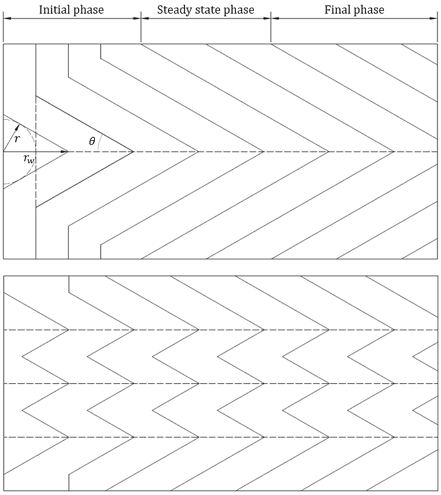
Schematic diagrams of burn-back process for propellant grains with embedded metal wires according to number of wires.
금속선이 삽입된 추진제 그레인의 burn-back은 연소면의 변화특성에 따라 3단계로 구분된다. 초기단계에서는 원뿔형태의 연소면이 생성되기 시작하고 연소면적이 시간에 따라 증가한다. 정상상태 구간은 원뿔형태의 연소면의 모선이 그레인 외경에 닿으면서 시작되는데, 해당구간에서의 연소면적은 시간에 따라 일정하게 유지된다. 말기단계에서는 삽입된 금속선은 모두 연소하고 남아있는 추진제가 연소되는 구간으로 연소면적은 시간에 따라 감소된다. 금속선의 개수를 증가시키는 경우 그레인의 burn-back 과정에서 초기단계로부터 정상상태단계로 넘어가는 시간은 줄어들고 정상상태구간에서의 연소면적은 금속선의 개수와 관계없이 동일하게 나타난다.
2.2 연소면 예측방법
추진제 그레인의 연소형상을 파악하기 위해서는 추진제 그레인 및 연소형상에 대한 좌표화가 필요하다. 본 논문에서는 원통형인 추진제 그레인의 중심을 3차원 직교좌표계의 z축에 일치시키고 연소가 시작되는 끝단 면에서의 연소방향을 z축의 음의 방향으로 두어 연소면 예측 및 연소면적 계산방법을 설명한다(Fig. 3 참조).
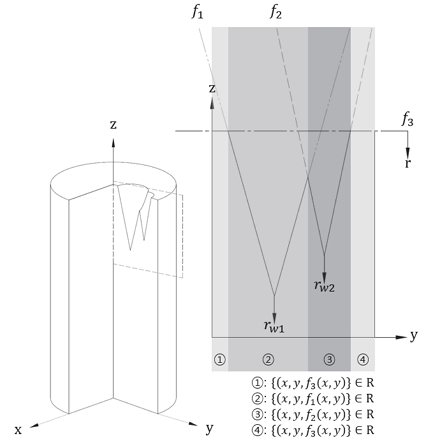
Schematic diagrams to explain a method which predict burning surface of a propellant grain with embedded metal wires.
금속선이 삽입된 추진제 그레인의 연소형상은 서로 다른 속도로(Fig. 3에서 rw1, rw2, r) 이동하는 도형들(Fig. 3에서 f1, f2, f3)로 구성되며, 각 도형들은 z = f(x, y) 형태인 도형함수로 나타낼 수 있다.
실제 연소면에 포함되는 점의 집합(R)은 원통형 추진제 그레인 원형면 내부의 임의의 x, y좌표에서 도형함수들의 z좌표 값들 중 최솟값을 가지는 점들로 구성된다.
연소말기단계에서는 임의의 x, y좌표에서 도형함수들의 z좌표가 추진제 그레인의 연소종료면의 z값 보다 작은 경우가 발생하는데, 이런 경우 연소면은 없는 것으로 판단한다.
2.3 연소면적 계산방법
금속선이 삽입된 추진제 그레인의 연소형상을 구성하는 도형들로 실제 연소면의 영역을 구분하였다. 구분된 영역(D)에서 도형의 면적(S)은 해당 도형함수의 적분식으로 표현 할 수 있다.
(1) |
도형면적에 대한 적분식을 풀어내어 구분된 영역에 따라 연소면적을 구하는 것이 정확한 연소면적을 계산하는 방법이지만, 연소면을 구성하는 서로 다른 도형들의 면적에 대한 적분식을 모두 풀어내는 것은 번거로운 일이며, 적분식을 풀어내기 어려운 경우 해당방법을 적용하기 어렵다.
본 연구에서는 연소면을 구성하는 서로 다른 도형들의 면적을 수치적으로 근사하는 방법을 사용했다. 추진제 그레인의 원형면 내부를 x-y평면 위에서 이산화한 뒤 실제 연소면을 사영시킨다. 오른쪽 위 끝점을 기준으로 격자들을 도형들의 영역에 따라 구분하였다(Fig. 4 참조). 도형면적에 대한 적분식은 아래와 같이 리만 합의 형태로 표현이 가능하며, 도형들의 영역에 따라 연소면적을 근사하였다.
(2) |
(3) |

Schematic diagrams to explain a method which calculate burning surface area of a propellant grain with embedded metal wires.
ΔA는 격자의 오른쪽 위 끝점을 기준으로 구분되는 격자의 면적크기이며, m, n은 각각의 점에 해당하는 x, y좌표의 수이다.
2.4 Burn-back 해석방법 적용대상
격자영향성과 금속선의 개수 및 위치에 따른 연소면적특성 분석이 수행되었다.
먼저, 격자 개수 증가에 따른 예측연소면적의 정확도 확인을 위한 격자영향성 분석이 수행되었다. 격자영향성 분석과정에서는 burn-back 해석방법을 검증하기 위해, 개발된 방법과 CAD 프로그램으로 연소과정에서의 그레인 형상을 직접 작도하는 방법으로 도출된 연소면적결과가 비교되었다. 개발된 방법은 MATLAB을 이용하여 작성하였으며, CAD 프로그램으로는 SOLIDWORKS를 사용하였다.
Fig. 5는 격자영향성 분석에서 사용된 그레인 형상이다. 금속선은 그레인의 원면이 접선방향으로 12등분이 되고 반경이 3등분이 되도록 24개가 배치되었다. 추진제 그레인의 연소전 형상은 길이 250 mm, 반경 50 mm인 원기둥이며 금속선의 연소속도 증가비는 5로 설정하였다.
추진제 그레인 외경에 위치한 격자들의 높이와 윗변의 길이가 동일하도록 설정하였고 전체 격자들의 반경방향의 크기(Δr)가 일치하도록 격자를 제작하였다.
금속선이 그레인의 원면을 접선방향으로 12등분하고 등분된 영역에서 금속선에서의 연소형상 발달이 동일하므로 등분된 영역에서만 계산을 수행하였고 획득되는 면적에 등분된 수를 곱하여 총 연소면적을 얻어냈다.
금속선의 삽입을 고려하지 않은 추진제의 연소거리가 1 mm 진행될 때 마다 연소면적을 얻어내도록 하였으며, Δr의 크기를 0.125 mm부터 4배씩 증가시켜 총 4가지 케이스에 대한 해석을 수행하였고 정확도 및 계산비용에 결과를 확인했다.
다음으로, 금속선의 개수 및 위치에 따른 연소면적 특성 분석을 수행하였다. 해당분석에서도 금속선의 연소속도 증가비와 추진제 그레인의 연소전 형상은 격자의존성 테스트와 동일하게 설정하였다. 금속선의 개수 및 위치에 따라 4가지 케이스를 선정하였으며, 해당정보는 Table 2에 기재하였다.
3. 결과 및 분석
3.1 격자 영향성 분석
Fig. 6에 Δr에 따른 연소면적의 계산결과와 CAD 프로그램으로부터 도출된 연소면적 결과를 비교했다. 연소거리(burning distance)는 금속선의 삽입을 고려하지 않은 추진제의 연소거리이다.
Table 3에 추진제의 연소거리에 따라 변화되는 금속선이 삽입된 추진제 그레인의 연소형상과 Δr에 따른 연소면적결과의 오차율(eN)을 나타냈다. 오차율은 CAD 프로그램에서 도출된 연소면적을 참값으로 가정하고 개발된 방법으로 도출된 결과와의 상대오차를 백분율로 나타낸 것이다.
3단계로 구분되는 금속선이 삽입된 추진제 그레인의 연소면의 변화특성(연소초기단계: 연소면적 증가, 정상상태단계: 연소면적 유지, 연소말기단계: 연소면적 감소)은 Δr이 가장 큰 case 4에서도 식별되었다.
정상상태 구간에서는 Δr에 관계없이 최초 연소면적에 연소속도 증가비를 곱한 만큼의 연소면적을 나타냈다. 연소속도 증가비가 동일한 금속선을 사용하면 정상상태에서 나타나는 연소형상은 동일한 원뿔도형만으로 구성된다. 원뿔면은 기하학적으로 원뿔면이 사영된 면에 연소속도 증가비를 곱한 값이 되고 정상상태단계에서의 면적은 Δr에 관계없이 최초연소면적에 연소속도 증가비를 곱한 만큼의 값을 가지게 된다.
연소초기 및 연소말기단계에서는 Δr이 작아지면서 오차율이 줄어들고 수렴하는 경향을 보였다. 격자들은 격자의 오른쪽 위 끝점을 기준으로 연소형상을 이루는 도형들의 영역에 따라 구분되고 특정 도형에 속한 격자들은 해당 도형의 면적만을 반영한다. 그러므로 격자가 도형들의 경계에 위치한 경우 실제 연소면적과의 오차가 발생되는데, Δr이 작을수록 오차는 작아지게 된다.
연소거리가 14 mm일 때 사용된 격자별 해석결과를 비교하면 Δr이 가작 작은 case 1의 경우 오차율은 0.189%까지 떨어지는 것을 확인 할 수 있었다.
Table 3에 그레인의 연소시작부터 종료까지의 연소면적을 획득하는데 걸리는 계산시간을 Δr에 따라 정리하였다. Intel I7-9700K가 사용되었으며 단일코어만을 사용하였다. 가장 오차율이 낮은 case 1의 경우 계산시간이 18초 수준으로 본 연구에서 개발된 방법으로 신속하게 금속선이 삽입된 추진제 그레인의 연소면적을 획득할 수 있음을 확인하였다. 이후 금속선의 개수 및 위치영향성 분석에서도 case 1에서 사용된 Δr을 사용하였다.
3.2 금속선의 개수 및 위치 영향성 분석
Fig. 7은 금속선의 개수 및 위치에 따른 연소면적의 계산결과를 나타낸다. 모든 case에서 동일한 연소속도 증가비를 가지는 금속선을 사용했기 때문에 정상상태에서 나타나는 연소면적의 크기는 금속선의 위치 및 개수에 관계없이 동일한 것이 확인되었다.
금속선의 개수증가에 따른 연소면적의 변화특성을 확인했다. Case 6에서는 case 5와 비교할 때, 같은 반경에 금속선의 개수가 두 배로 증가되었다. 금속선의 개수가 증가되면서 연소초기 및 말기단계가 짧아지고 정상상태구간이 길어지는 것을 확인 할 수 있었다. 금속선의 수가 증가되면 원뿔형으로 발달되는 연소형상의 수가 증가되어 원뿔형 연소형상만으로 구성되는 정상상태구간에 일찍 도달하게 되고 연소 초기와 말기구간이 짧아진다.
금속선의 위치에 따른 연소면적의 변화특성을 확인했다. Case 6, 7에는 동일한 수의 금속선이 삽입되었는데, case 6에서는 추진제 그레인의 반경을 2등분하는 위치에 12개의 금속선이 삽입되었고 case 7에서는 추진제 그레인의 반경을 3등분하는 위치에 6개씩 금속선이 삽입되었다. Case 7에서는 case 6 대비, 연소초기 영역에서의 연소면적이 급증하고 연소말기에서 연소면적이 급감하는 것으로 나타났다. 서로 다른 반경에 금속선을 배치할 경우 동일한 반경에 금속선을 배치시키는 경우보다 효율적으로 끝 단면 연소형상을 원뿔형 연소형상으로 전환시키기 때문에 연소 초기와 말기에 급격한 연소면적 변화가 있는 것으로 판단된다.
일반적으로 정상상태 구간이 길고 연소초기와 말기가 짧은 추력설계가 요구되는데 효율적으로 금속선의 위치 및 개수를 선정하는 것이 주요 설계변수가 될 것으로 판단된다.
4. 결 론
금속선이 삽입된 추진제 그레인의 연소면을 예측하고 연소면적을 계산하는 방법이 개발되었다. 연소면은 3차원 직교좌표계에서 함수로 표현이 가능한 도형들로 구성되며, 실제 연소면은 동일한 x, y좌표에서 도형함수들의 z좌표 값들 중 최솟값을 가지는 점들로 구성된다. 연소면적은 적분식으로 표현되는 도형면적함수를 리만합으로 표현하고 수치적으로 근사하여 도출했다.
개발된 burn-back 해석방법의 격자영향성 분석이 수행되었다. 정상상태에서의 연소면적은 Δr과 관계없이 최초연소면적에 연소속도 증가비를 곱한 값으로 나타났다. 연소초기 및 말기단계에서는 Δr이 줄어들수록 계산되는 연소면적의 오차율이 줄어들면서 수렴하는 경향을 보였다.
금속선의 개수 및 위치에 따른 연소면적 특성을 확인했다. 금속선의 위치 및 개수와 관계없이 정상상태 구간에서 연소면적의 크기는 동일한 것이 확인되었다. 금속선의 개수가 증가함에 따라 연소초기 및 말기 구간이 짧아지고 정상상태구간이 길어지는 것이 확인되었다. 동일한 개수의 금속선을 삽입할 때, 서로 다른 반경에 금속선을 위치시키는 경우에서 동일한 반경에 금속선을 위치시키는 경우보다 연소초기 영역에서의 연소면적이 급증하고 연소말기에서 연소면적이 급감하는 것이 확인되었다.
요구되는 추력을 설계함에 있어 적절한 금속선의 개수 및 위치를 선정하는 것이 중요한 과정이 될 것으로 보이며 실제 금속선이 삽입된 추진제 그레인을 사용하는 추진기관의 추력설계과정에서 금속선의 위치 및 개수에 대한 최적화 연구가 수행될 예정이다.
Acknowledgments
[이 논문은 한국추진공학회 2021년도 추계학술대회(2021.11.24.∼26, 웨스틴 조선호텔 부산) 발표논문을 심사하여 수정ㆍ보완한 것임.]
References
- Rumbel, K.E. and Cohen, M., “Propellant grains,” U.S. Patent 3109374, Nov. 1963.
-
Sparks, J.F. and Friedlander III, M.F., “Fifty years of solid propellant technical achievements at Atlantic Research Corporation,” 35th Joint Propulsion Conference and Exhibit, Los Angeles, C.A., U.S.A., AIAA 1999-2932, Jun. 1999.
[https://doi.org/10.2514/6.1999-2932]
-
Caveny, L.H. and Glick, R.L., “Influence of embedded metal fibers on solid-propellant burning rate,” Journal of Spacecraft and Rockets, Vol. 4, No. 1, pp. 79-85, 1967.
[https://doi.org/10.2514/3.28813]
-
Gossant, B., Godfroy, F. and Robert, P.H, “Theoretical calculus of burning rate ratio in grains with embedded metal wires,” 34th Joint Propulsion Conference, Boston, M.A., U.S.A., AIAA 1988-3255, Jul. 1988.
[https://doi.org/10.2514/6.1988-3255]
-
King, M.K., “Analytical modeling of effects of wires on solid motor ballistics,” Journal of Propulsion and Power, Vol. 7, No. 3, pp. 312-321, 1991.
[https://doi.org/10.2514/3.23329]
- You, J.C., Park, Y.K. and Kim, I.C., “Combustion characteristics of composite solid propellants embedded with metal wires,” Journal of the Korean Society for Aeronautical & Space Sciences, Vol. 26, No. 2, pp. 133-142, 1998.
- You, J.C., “Burning characteristics of nitramine propellant embedded with metal wires,” Journal of the Korean Society of Propulsion Engineers, Vol. 4, No. 4, pp. 50-58, 2000.
-
Kubota, N. and Ichida, M., “Combustion processes of propellants with embedded metal wires,” AIAA Journal, Vol. 20, No. 1, pp. 116-121, 1982.
[https://doi.org/10.2514/3.51056]
- Hyun, H.S., Hwang, K.S. and Kim, C.K., “Combustion behavior of solid rocket motor embedding silver wire in propellant,” Journal of the Korean Society for Aeronautical & Space Sciences, Vol. 26, No. 3, pp. 115-122, 1998.
- You, J.C., Park, Y.K. and Kim, I.C., “A study on the burning characteristics of N-5 propellant embedded with metal wires,” Journal of the Korean Society of Propulsion Engineers, Vol. 3, No. 3, pp. 78-85, 1999.
-
Isert, S., Lane., C.D. and Gunduz, I.E., Son, S.F., “Tailoring burning rates using reactive wires in composite solid rocket propellants,” Proceedings of the Combustion Institute, Vol. 36, No. 2, pp. 2283-2290, 2017.
[https://doi.org/10.1016/j.proci.2016.06.141]
-
Collard, D.N., McClain, M.S., Fleck, T.J., Rahman, N.A., Rhoads, J.F., Meyer, T.R. and Son, S.F., “Solid propellant with embedded additively manufactured reactive components,” AIAA Propulsion and Enrgey 2019 Forum, Indianapolis, I.N., U.S.A., AIAA 2019-4443, Aug. 2019.
[https://doi.org/10.2514/6.2019-4443]
-
Collard, D.N., Fleck, T.J., Rhoads, J.F. and Son, S.F., “Tailoring the reactivity of printable Al/PVDF filament,” Combustion and Flame, Vol. 223, pp. 110-117, 2021.
[https://doi.org/10.1016/j.combustflame.2020.09.016]
-
Barkley, S.J., Kindem, D.K., Zhu, K., Michael, J.B. and Sippel, T., “Dynamic control of composite solid propellant flame spread through microwave eddy current heating of propellant-embedded antennas,” AIAA SciTech Forum, San Diego, C.A., U.S.A., AIAA 2019-1239, Jan. 2019.
[https://doi.org/10.2514/6.2019-1239]
-
Oh, S.H., Lee, H.J. and Roh, T.S., “Development of a hybrid method in a 3-D numerical burn-back analysis for solid propellant grains,” Aerospace Science and Technology, Vol. 106, 106103, 2020.
[https://doi.org/10.1016/j.ast.2020.106103]
-
Park, C.W., Roh, T., Lee, H.J. and Jung, E., “Analysis of burn-back tendency on the Finocyl grain,” Journal of the Korean Society of Propulsion Engineers, Vol. 25, No. 2, pp. 55-65, 2021.
[https://doi.org/10.6108/KSPE.2021.25.2.055]