
한국형발사체 성능 고도화 핵심기술 검증을 위한 고압 축소형 연소기 개발
Copyright Ⓒ The Korean Society of Propulsion Engineers
This is an Open-Access article distributed under the terms of the Creative Commons Attribution Non-Commercial License(http://creativecommons.org/licenses/by-nc/3.0) which permits unrestricted non-commercial use, distribution, and reproduction in any medium, provided the original work is properly cited.
초록
한국형발사체용 연소기 성능 고도화를 위한 핵심기술을 검증하기 위해 고압 축소형 연소기를 개발하였다. 성능 고도화를 위한 핵심기술은 고압 연소기용 분사기 설계, 적층제조기법을 적용한 연소안정화 장치 개발, 고압 축소형 연소기 헤드 및 재생냉각 연소실 설계/제작 등이다. 고압 축소형 연소기 개발을 통해 핵심기술을 검증하였고, 이 기술들은 향후 대형 액체로켓엔진 연소기 개발에 활용될 예정이다.
Abstract
In this study, a high-pressure subsacle thrust chamber was developed to verify the core technology for KSLV-II performance enhancement. The core technologies are the design of an injector for high-pressure combustion, development of a combustion stabilization device using the additive manufacturing technique, and the design and fabrication of mixing head and regeneratively cooled combustion chamber. The core technologies, which have been verified through the development of high-pressure subscale thrust chamber, will be used to develop large engine liquid rocket engine thrust chamber in the future.
Keywords:
Subscale Thrust Chamber, Liquid Rocket Engine, Performace Enhancement, KSLV-II키워드:
축소형 연소기, 액체로켓엔진, 성능 향상, 한국형발사체1. 서 론
2018년 11월 28일 누리호 시험발사체가 나로 우주센터에서 발사되었고 3단형 한국형발사체(KSLV-II)의 본 발사를 앞두고 있다. 한국형발사체개발사업을 통해 75톤급 엔진의 개발이 완료 단계에 있으나 경쟁력 있는 해외 우주발사체 엔진과의 기술적 격차는 분명 존재한다. 즉 경쟁력 있는 발사체를 확보하기 위해서는 무엇보다도 발사체 성능의 핵심인 액체로켓엔진의 성능 고도화가 필수적이라고 할 수 있다. 한국형발사체 75톤급 엔진의 연소압력은 6.0 MPa 수준으로 이는 해외 부스터급 가스발생기 사이클 엔진의 연소압력과 비교 시 낮은 수준이다. 예로 SpaceX는 기존 연소압 6.1 MPa의 Merlin-1C 엔진에서 9.7 MPa의 Merlin-1D 엔진으로 개선하여 고성능, 저비용, 그리고 재사용의 발사체를 개발하였다. 이에 한국형발사체 75톤급 엔진의 성능 고도화를 위해서는 연소압 10 MPa 수준으로의 고압화가 필요하며, 관련한 핵심기술에 관한 선행연구가 필요하다. 고압화에 필요한 핵심기술들을 분석, 개발하여 이를 축소형 연소기에 적용, 시험 평가를 통해 각 핵심기술을 검증하였다.
2. 고압 축소형 연소기 설계 및 제작
2.1 연소기 고압화 핵심기술
한국형발사체용 75톤 및 7톤 연소기의 개발 경험을 바탕으로 연소압 10 MPa 수준의 고압화를 위해서 다음과 같은 핵심기술들의 선행개발이 필요하다고 판단하였다.
- ▪ 고압 분사기 설계 기술
- ▪ 고성능/저비용/재사용 엔진에 적합한 적층제조기법(Additive Manufacturing, AM)을 적용한 연소안정화 장치(배플분사기) 설계/제작 기술
- ▪ 고압 연소기 냉각(재생냉각/막냉각/코팅) 설계 기술
- ▪ 고압 연소기 제작 및 연소시험을 통한 핵심기술요소 검증
2.2 고압 연소기(실물형/축소형) 성능 규격 및 형상 설계
한국형발사체 75톤급 엔진의 진공 비추력은 298.6초로 SpaceX사의 Merlin-1D 311초에 비해 낮은 값이고, 또한 엔진 추력/중량 비(T/W) 또한 상당히 낮아 고압화를 통한 비추력 성능 향상과 더불어 경량화가 필요하다. 이에 한국형발사체 75톤급 엔진 연소기를 SpaceX사의 Merlin-1D 급 수준의 성능 향상을 목표로 성능 규격을 도출하였다. 도출한 고압 실물형 연소기는 케로신 계열의 탈황/탈방향족 연료유와 액체산소를 추진제로 사용하는 가스발생기 사이클의 부스터급 재생냉각 연소기로 정격 연소압은 10 MPa, 혼합비는 2.5이다. 노즐팽창비는 요구되는 진공 비추력 및 75톤 엔진 연소기의 노즐 직경을 벗어나지 않는 조건 등을 고려하여 19.6으로 결정하였다. 추진제 유량은 75톤 엔진 연소기 대비 약 4% 증가하였고, 연소압력이 증가함에 따라 연소기 직경 및 노즐목 직경은 다소 감소하였다. 고압 실물형 연소기 형상은 크게 헤드부와 추력실부로 구성되며, 전반적인 형상 및 구성은 한국형발사체 75톤 1단 연소기와 유사하다. 헤드부의 분사기는 동축와류형 분사기를 적용하여 총 14열의 배열로 설계하였으며, 확대 노즐부를 포함한 추력실부 전체에 냉각 채널을 구성하고 연료에 의한 재생냉각 및 막냉각을 적용하였다. 초음속 노즐부는 80% 벨(bell) 노즐로 설계하였으며 진공 비추력이 최대가 되는 노즐 형상을 도출하였다.
고압 축소형 연소기는 기본적으로 고압 실물형 연소기에 적용할 동축와류형 분사기의 검증을 목적으로 설계하였다. 고압 축소형 연소기의 추력 및 노즐 팽창비는 연소시험설비에서 안전하게 연소시험을 수행할 수 있는 수준으로 설정하였다. 고압 축소형 연소기 헤드면은 고압 실물형 연소기 헤드면의 일부를 모사할 수 있도록 분사기 간의 간격을 실물형과 동일하게 하면서 3열로 배열하였고, 전체 혼합비가 2.5가 되도록 추진제 유량을 결정하였다. 또한 추력실 내측 코팅 소재 및 막냉각 위치 등에 대하여 고압 실물형 연소기와 유사한 설계를 적용하면서 추력실부를 냉각하고 헤드부로 유입되는 연료의 온도 조건까지 모사하도록 설계하였다. 고압 실물형 및 축소형 연소기의 기본 특성을 Table 1에 간략히 나타내었으며, 추력실부 내측 형상을 Fig. 1에 나타내었다.
2.3 고압 분사기 설계
분사기는 연소기의 연소성능 및 연소안정성에 큰 영향을 미치는 구성품으로 고압 연소기에 적용할 분사기는 동축와류형 분사기 2종으로 설계하였고, 시험 평가를 통해 최종적으로 1종을 선택하고자 하였다. Fig. 2에 2종의 동축와류형 분사기의 개략도를 나타내었다. Type 1은 한국형발사체 75톤급 연소기에 적용한 분사기로서 고압 연소기에 적용 시 분사기당 단위 유량이 391 g/s로 기존 75톤급 연소기의 분사기당 단위 유량보다 약 11% 증가하였다. 동일한 분사기 형상에서 유량이 증가함에 따른 차압 증가분은 약 0.3∼0.5 MPa이다. 분사기당 단위 유량 및 차압 증가분을 고려했을 때 고압 연소기용 분사기로서 적용 가능할 것으로 판단되었다. Type 2는 Type 1과 산화제 측 설계는 동일하고, 연료 측 분사기 형상 계수(geometrical constant, K)와 분무각(spray angle)을 증가시키는 설계안을 적용 하였다. 이는 일부 해외 엔진 연소기에 적용한 분사기 설계를 반영한 것으로 type 1과 비교하여 연료측 설계 변경에 따른 특성 차이를 확인할 수 있을 것으로 판단되었다.
분사기의 여러 설계 인자 중 연소성능과 밀접한 관련이 있는 인자는 분사기의 리세스 길이(recess length) 혹은 리세스 수(recess number) 로 정의되는 인자이다. 리세스 길이는 산화제 노즐 끝단에서 연료 노즐 끝단까지의 거리이며, 리세스 수는 위의 리세스 길이와 산화제 분무막이 연료 분무막과 만나는 지점까지의 거리와의 비를 의미한다. 기존 연구에서 리세스 수 증가에 따라 추진제의 혼합특성이 외부혼합에서 내부혼합으로 변화됨에 따라 연소성능 지표로 표현되는 연소특성속도(characteristic velocity)는 증가하는 결과를 보였다[1,2]. 고압 연소기용 분사기도 기본 리세스 수인 0.6에서부터 1.0, 1.25, 1.5까지 변화시켜 각각의 연소성능 및 특성을 비교하고자 하였다.
2.4 적층제조기법을 적용한 연소안정화 장치 개발
한국형발사체 엔진 연소기에 적용된 연소안정화 장치는 개별 분사기의 형태를 갖는 배플분사기이다. 현재 적용하고 있는 배플형상이 각각 하나의 개별 분사기로 구성되기 때문에 초기 점화 충격에 구조적으로 다소 취약하고, 또한 제작상 내피부와 외피부의 브레이징 접합공정의 한계에 따른 국부적인 열변형 및 열손상이 발생할 가능성이 크다. 이러한 단점이 존재하는 배플분사기를 고추력/고팽창비/고압 연소기에 그대로 적용할 경우 위의 단점들이 더욱 심화될 수 있기에 이를 원천적으로 극복할 수 있는 새로운 설계가 요구되었다. 이에 기존의 개별 분사기가 아닌 일체형 구조를 가지며, 기계 가공 방식이 아닌 적층제조기법을 활용한 배플분사기를 개발하여 열내구성과 구조적 강건성을 향상시켰다. Fig. 3에 기존 제작 방식의 개별 배플분사기와 AM 방식의 일체형 배플분사기를 나타내었다. 산화제 공급관을 통해 유입된 산화제는 두 개의 유로로 분기되어 스크류(screw) 및 노즐을 통해 선회 운 동량을 갖는 중공원형(hollow cone) 형태로 분사된다. 연료는 연료 매니폴드 부에서 유입 홀을 통해 유입된 후 일정 각도를 갖는 나선형 냉각 채널을 통해 흐르면서 외부 벽면을 냉각시킨다. 냉각 채널을 통과한 연료는 배플 끝단 컬렉터(collector)에 모여 다수의 분사 홀을 통해 제트(jet) 형태로 분무 된다. 배플 길이는 고압 실물형 연소기에 적용하는 것으로 고려하여 70 mm로 설계하였다. AM 방식의 일체형 배플분사기 소재는 인코넬 625를 적용하여 고온 및 고압에서 구조적으로 안정하도록 하였다. 몇 개의 시편을 제작하여 Fig. 4와 같이 수력학적 특성 평가시험을 통해 최종 설계를 확정하였고, 고압 축소형 연소기 헤드부에 적용하였다.
2.5 고압 연소기 헤드부 및 추력실부 냉각 설계
고압 축소형 연소기 헤드부는 위에서 언급한 고압 분사기 type 1과 type 2를 각각 적용한 헤드부 2종(SDM1/SDM2)과 type1 분사기와 AM 방식의 일체형 배플분사기를 적용한 헤드부 1종(SDM3), 총 3종의 헤드부를 설계하였다. 2종의 주분사기 검증 및 AM 배플분사기의 열내구성 검증 등을 위해 헤드부와 추력실부는 조립/분리가 가능하되 추력실부를 냉각한 연료가 헤드부로 유입되는 구조로 설계하였다.
고압 연소기 추력실부는 전체를 냉각 채널로 구성하고 연료에 의한 재생냉각 및 막냉각을 적용하였다. 배플분사기 끝단과 인접한 지점과 축소부가 시작되는 지점에 링 형태의 1차 및 2차 막냉각부를 각각 배치하였다. 고압 축소형 연소기의 막냉각 유량은 고압 실물형 연소기 작동 조건에서의 주분사기 유량 조건을 만족하도록 전체 연료 유량의 15.4%로 결정하였고, 1차 및 2차 막냉각 유량비는 실물형 연소기와 동일하게 3 : 7로 적용하였다. Fig. 5에서 냉각을 위한 연료는 2곳에서 공급되는데 벽면 열유속이 가장 높은 구간인 노즐목 근처에서의 채널 냉각 효과를 높이기 위해 노즐목부로 공급되어 노즐목부와 확대노즐부를 냉각한 후 노즐 끝단에서 모두 연소기 외부로 배출되도록 설계하였다. 나머지 1곳은 실린더부 끝단에서 공급되어 일부 유량은 바로 2차 막냉각으로 공급되고 실린더부를 냉각한 후 1차 막냉각으로 일부 공급되고 나머지는 실린더부 앞단에서 빠져나와 헤드부 연료 유입부로 연결된 배관을 따라 헤드부로 공급된다. 추력실 내피는 동합금 소재를 적용하였으며 산화를 방지하기 위해 실물형 연소기에서와 동일하게 확대 노즐부를 포함한 전체 내벽에 니켈-크롬(Ni-Cr) 코팅을 적용하였다.
3. 시험 평가
3.1 연소시험 조건 및 수행
제작된 고압 축소형 연소기는 Fig. 6과 Fig. 7에서와 같이 설계점 및 탈설계점 조건에서 연소시험을 통해 적용된 핵심기술들을 검증하였다. 시험조건 및 회수는 각 헤드부 당 설계점(연소압 10 MPa, 혼합비 2.5) 2회, 탈설계점(연소압 10 MPa ± 7%, 혼합비 2.5 ± 7%)에서 4회 등 총 5회 연소시험을 1set로 구성하였다. 각 헤드부의 주분사기 리세스 수는 기본적으로 0.6이며, 1set의 시험이 완료되면 리세스 수를 1.0으로 수정 가공하여 다시 1set의 연소시험을 수행하였다. 이런 방식으로 리세스 수를 1.25, 1.5까지 수정가공하면서 시험을 진행하였다. 모든 헤드부는 하나의 추력실부와 조립하여 시험을 수행함에 따라 헤드부만의 차이(주분사기 연료측 형상 및 리세스 길이, 배플분사기 유무 등)에 따른 특성 비교가 가능하도록 하였다. 수행된 연소시험은 총 63회, 누적시간 765초이다. SDM1은 계획된 모든 시험을 수행하였으나 SDM2는 리세스 수 0.6, 1.0까지만 진행하였고, AM 배플분사기가 적용된 SDM3는 리세스 수 1.5에서는 설계점 조건의 시험만 수행되었다. SDM3의 연소시험은 총 20회, 누적시간 290초이며 단일 최장 100초 연소시험을 통해 AM 배플분사기의 열내구성을 확인하였다.
3.2 연소 성능
고압 축소형 연소기의 시험결과를 연소성능 및 연소안정성 측면에서 살펴보았다. Fig. 8에 설계점 조건에서 3종의 헤드부, 그리고 각 헤드부의 주분사기 리세스 수에 따른 특성속도효율(characteristic velocity efficiency)을 나타내었다. 우선 헤드부에 따른 성능을 비교해보면 주분사기의 연료측 설계가 다른 SDM1과 SDM2는 주분사기의 리세스 수 0.6, 1.0에서 성능이 거의 동일함을 보였다. 연료 분사기의 형상계수와 분무각을 증가시키는 설계는 연소성능에는 영향을 주지 않고, 차압을 약 0.3 MPa 증가시켰다. SDM1과 SDM3는 주분사기는 동일하고, 배플분사기의 유무 차이만 있는데 배플분사기가 장착된 SDM3가 모든 리세스 수에서 SDM1 보다 높은 성능을 보였다. 이는 추진제 혼합특성의 관점에서 보면 배플분사기가 주분사기 사이의 격벽으로 작용함으로써 분사기들간의 추진제 혼합효율을 저감시킬수 있음에도 불구하고 배플분사기 끝단에서 산화제와 연료의 혼합특성이 양호함에 따른 결과라 판단된다. 최대 특성속도효율은 AM 배플이 장착된 SDM3의 리세스 수 1.25에서 약 96%로 나타났다. 이때 연소기 내측 벽면 냉각을 위한 막냉각 유량이 설계 유량 대비 약 20%가 더 유입된 점을 고려한다면 목표효율인 96.4%는 달성할 것으로 판단된다. 위에서도 언급하였듯이 기존 연구결과에 따르면 분사기의 리세스 수 증가에 따라 특성속도효율은 증가함을 보인다. 본 고압축소형 연소기의 경우 리세스 수 0.6에서부터 1.25까지는 기존 결과의 경향과 유사하게 특성속도효율이 증가함을 보였으나 리세스 수 1.5에서는 오히려 다소 감소함을 보였다. 이러한 결과는 SDM1과 SDM3에서 모두 동일하게 나타났다. 리세스 수가 증가함에 따라 추진제의 내부혼합특성이 혼합효율을 증가시키고 그 결과 연소성능이 향상하는 것으로 보이나 이러한 경향에도 어떤 한계점(threshold)이 있는 것으로 판단된다. 어떤 인자가 그 한계에 영향을 주는 것인지에 대해서는 좀 더 추가적인 연구가 필요하다. Fig. 9는 탈설계점 조건에서의 결과인데 탈설계점 조건에 따른 특성속도효율의 경향성은 크게 나타나지 않았고, 설계점 결과와 유사하게 리세스 수가 증가함에 따라 효율이 증가함을 보였다. 또한 리세스 수 1.25에서 1.5로 증가할 때 SDM1의 OD3(고압/고혼합비) 조건의 결과를 제외하고는 모두 효율이 증가함을 보였다. Fig. 10은 연료가 연소기로 유입되어 실린더부의 재생냉각 채널을 따라 냉각을 한 후 헤드부로 유입될 때의 온도 상승을 나타낸 것인데 리세스 수 1.0에서 1.25로 증가함에 따라 연료 온도가 급격히 상승함을 보였다. 내부혼합의 특성을 갖는 분사기가 연소성능을 향상시키고 동시에 벽면 열유속도 증가시킴을 확인할 수 있었다.

Variations of combustion efficiencies with respect to a recess number for high pressure thrust chamber at design point condition.
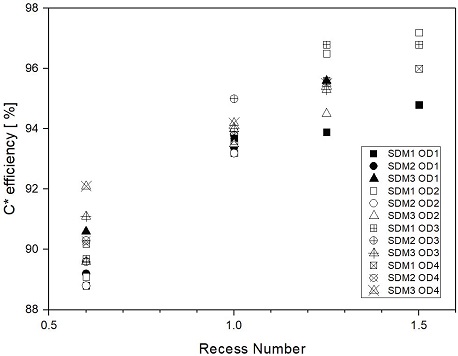
Variations of combustion efficiencies with respect to a recess number for high pressure thrust chamber at off-design point conditions.
3.3 연소안정성
연소실에 동압센서를 장착, 연소시험 시 압력 섭동을 측정하여 연소안정성을 확인하였다. 압력 섭동의 RMS(Root Mean Square) 값과 연소압력의 비(p’rms/pc)로 연소안정성을 평가하는데 이를 정적평가(static assessment)라 한다. 여러 문헌마다 그 기준값이 조금씩은 상이하나 여기서는 약 3%를 기준값으로 판단하였다[3-6]. Fig. 11에 모든 고압 축소형 연소기에 대해 정격 연소압력과 혼합비로 각각 정규화된 연소압력과 혼합비에 따른 섭동 비율의 크기를 비교하였다. 작동조건에 따른 영향은 연소압력이 증가할수록 섭동의 크기가 다소 증가함을 보였고, 특히 고압/고혼합비 조건(OD3)에서 섭동의 크기가 상대적으로 증가하였다. SDM2의 경우 리세스 수 1.0일 때 OD3 조건 시험에서 약 7.04%의 상당히 큰 압력 섭동이 나타났다. 설계점 조건에서 SDM2 리세스 수 0.6과 1.0에서의 연소성능이 SDM1과 유사한 수준임이 확인되었고, 또한 이런 큰 압력 섭동이 나타남에 따라 리세스 수정 가공을 통한 더 이상의 시험은 수행하지 않았다. SDM2의 OD3 결과를 제외하고는 모두 3% 이하의 섭동 비율을 보였고, 설계점 조건에서는 약 1.2% 내외의 값을 보여 상당히 안정적인 연소가 이루어졌다. SDM1과 SDM3의 리세스 수에 따른 섭동 비율의 크기는 Fig. 12와 Fig. 13에 각각 나타내었다. 리세스 수 증가에 따른 섭동 비율의 크기가 두 종류의 헤드부에서 일치된 경향이 나타나지는 않았으나 한가지 공통된 경향은 리세스 수 0.6/1.0 보다 1.25/1.5일 때 압력 섭동 비율이 낮음을 보였다. 즉, 두 헤드부 모두 주분사기의 외부혼합보다는 내부혼합의 특성을 보일 때 좀 더 안정적인 연소가 이루어짐을 보였다. 설계점 조건에서는 두 헤드부 모두 리세스 수 1.25에서 압력 섭동 비율이 가장 낮았다. 이로써 연소성능 및 연소안정성 측면을 고려했을 때 가장 적합한 주분사기는 type 1의 리세스 수 1.25라고 판단된다. 배플 유무에 따른 섭동 비율의 크기는 특별한 경향성은 나타나지 않았고, 배플의 연소안정성 영향은 정적평가 보다는 SRT(Stability Rating Test)와 같은 동적 평가(dynamic assessment)를 통해 추후 검증되어야 할 것이다.
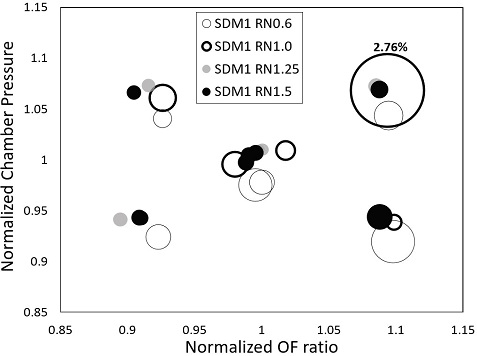
RMS values of pressure fluctuation normalized by a static chamber pressure with respect to a recess number for SDM1.
3.4 시험 후 HW 상태
시험 후 주분사기를 포함한 헤드부, AM 배플분사기, 추력실부 및 벽면 코팅 상태 등을 살펴보았다. 우선 각 헤드부에서 주분사기 및 헤드면의 상태는 양호했고, 특히 리세스 수가 증가함에 따라 열부하가 증가하는 산화제 포스트(post)의 열변형은 나타나지 않았다. 기존의 개별 배플분사기에 비해 열내구성과 구조적 강건성을 증가시킨 AM 배플분사기의 연소시험 후 상태를 Fig. 14에 나타내었다. 추진제가 분무되는 배플 끝단의 상태는 매우 양호하였다. 배플 끝단 모서리 부분에서의 열손상은 보이지 않았고, 배플 측면도 기존 배플분사기에서 나타났던 외피부 열손상은 보이지 않았다. 다만 배플과 배플이 맞닿는 안쪽 모서리 부분(Fig. 14의 원형표시 부분)에서 열손상이 나타났다. 이 부분은 냉각 채널 내벽 두께가 다른 영역에 비해 더 두꺼운 영역으로 이는 향후 간단한 설계수정을 통해 내벽 두께 다소 낮추면 해결이 가능할 것으로 판단된다. 추력실부의 실린더 내벽에서는 열손상 및 코팅의 크랙이나 박리 등은 확인되지 않았다. 그러나 Fig. 15와 같이 노즐목부에서는 벽면 코팅의 크랙이 180° 간격으로 나타났고(Fig. 15 원형 표시 부분), 이 상태에서 시험이 지속됨에 따라 코팅 크랙이 심한 부분에서 최종적으로 내피 동합금 소재가 열손상을 입어(Fig. 15 사각형 표시 부분) 냉각 채널의 연료유가 누유되었다. 노즐목부에서 180° 간격으로 코팅의 크랙이 발생된 원인은 노즐목부 내피부와 외피부의 조립 및 접합을 위해 그 사이에 구조물(bush)이 삽입되는데 이 구조물은 2개의 파트로 구성되어 있다. 이 구조물이 양쪽에서 노즐목부 내피부를 감싸고 그 위에 외피부가 조립되어 접합되는 구조로 되어 있다. 이 두 개의 구조물 사이의 틈새에서 내피의 동합금 소재가 반복되는 연소시험으로 인해 팽창 및 수축이 반복됨에 따라 코팅의 크랙이 발생하였고, 냉각성능이 떨어짐에 따라 그 부분의 내피부가 손상된 것으로 파악된다. 이러한 노즐목부 내피부와 외피부의 조립을 위해 두 개의 파트로 구성되는 구조물을 삽입하여 제작하는 방식은 실제 비행용 연소기에는 적용하지 않는 제작 방식이다. 비행용 연소기에 적용하는 제작 방식은 내피 동합금 소재를 여러 치구를 이용하여 노즐목 이후를 노즐 형상으로 변형시키는 벌징(bulging) 방식[7]을 적용하기 때문에 위와 같은 국부적인 코팅 크랙은 발생하지 않을 것으로 판단된다. 이러한 제작 방식은 현재 한국형발사체용 연소기에 적용하고 있다.
4. 결 론
한국형발사체 75톤급 엔진의 성능 고도화를 위해 연소압 10 MPa 수준으로의 고압화가 필요하며, 관련한 핵심기술에 관한 선행연구가 필요하다. 고압화에 필요한 핵심기술들을 분석, 개발하여 이를 축소형 연소기에 적용, 시험 평가를 통해 각 핵심기술을 검증하였다. 검증과정을 통해 나타난 몇 가지 문제점들은 충분히 해결 가능할 것으로 판단되며 이러한 핵심기술들은 향후 고성능 실물형 연소기 개발에 적극적으로 활용될 예정이다.
Nomenclature
AM : | Additive manufacturing |
OD3 : | Off-design point 3 |
RMS : | Root mean square |
SRT : | Stability rating test |
Acknowledgments
[이 논문은 한국추진공학회 2021년도 춘계학술대회(2021. 5. 26-28, 라마다프라자 제주호텔) 발표논문을 심사하여 수정·보완한 것임.]
References
- Seo, S., Han, Y.M., Kim, S.H., Seol, W.S. and Lee, S.Y., “Combustion Dynamic Behavior of Bi-Liquid Double Swirl Coaxial Injectors,“ AJCPP, Japan, AJCPP2005-22052, 2005.
- Seo, S., Lee, K.J., Han, Y.M., Kim, S.H., Kim, J.G., Moon, I.Y. and Seol, W.S., “Study on Combustion Characteristics of Unielement Thrust Chambers with Various Injectors,“ Journal of the Korean Society of Propulsion Engineers, Vol. 8, No. 2, pp. 85-94, 2004.
- Klem, M.D. and Fry, R.S., “Guidelines for Combustion Stability Specifications and Verification Procedures for Liquid Propellant Rocket Engines,” Tech. rep., CPIA Publication 655, January 1997.
- Lourme, D.(Chapter 1), Priem, R. and Breisacher, K.(Chapter 8), “Combustion Instability in Liquid Rocket Engines,” ESA WPP-062, 1993.
- Sutton, G.P. and Biblarz, O., Rocket Propulsion Elements, 7th ed., John Wiley & Sons Inc., New York, U.S.A., 2001.
- Seo, S., Lee, K.J. and Choi, H.S., “Study on Standards of Combustion Stability Assessment of Liquid Rocket Engine Combustion Devices,“ Journal of the Korean Society of Propulsion Engineers, Vol. 13, No. 6, pp. 34-40, 2009.
- Ryu, C.S. and Choi, H.S., “Development of Bulging Process for Regenerative Cooling Nozzle of Liquid Rocket Engine Thrust Chamber,“ Aerospace Engineering and Technology, Vol. 7, No. 2, pp. 103-109, 2008.