
연소기 산화제 개폐밸브 재순환예냉 유로의 유량계수 개선
Copyright Ⓒ The Korean Society of Propulsion Engineers
This is an Open-Access article distributed under the terms of the Creative Commons Attribution Non-Commercial License(http://creativecommons.org/licenses/by-nc/3.0) which permits unrestricted non-commercial use, distribution, and reproduction in any medium, provided the original work is properly cited.
초록
본 논문에서 극저온 추진제를 사용하는 액체추진기관의 재순환예냉 시스템 설계의 유연성을 확보하기 위한 연소기 산화제 개폐밸브 재순환예냉 유로의 유량계수 개선 내용을 소개하였다. 밸브의 재순환예냉 출구 포트 크기와 밸브 내부 유로 형상 변경에 의한 재순환예냉 유로의 유량계수 값을 예측하기 위해서 기존 밸브에서 측정한 재순환예냉 유로의 유량계수 값들을 활용하였으며, 액체질소를 운용유체로 사용하여 측정한 유량계수와 예측값과의 비교를 통해 밸브 내부 형상 변경에 의한 유량계수 개선정도를 확인하였다. 연소기 산화제 개폐밸브의 재순환예냉 유로의 유량계수는 기존 밸브에 비해 2배가량 향상되었으며, 결과적으로 연소기 산화제 개폐밸브에 할당되었던 설계 요구 차압의 75%가량을 재순환예냉 시스템에서 추가적으로 소요될 수 있는 잠재적인 차압과 재순환예냉 시스템의 다른 구성품의 추가 차압으로 활용될 수 있을 것으로 기대된다.
Abstract
The improvement of a flow coefficient for the recirculation chill-down flow in a main oxidizer shut-off valve has been presented. The flow coefficient, which is mainly affected by the recirculation outlet port size and the configuration inside the valve, has been predicted with measured flow coefficient values. The comparison of experimentally measured flow coefficient with the predicted value shows the effect of valve inside configuration on the flow coefficient. Consequently, the flow coefficient is twice the previous value and about 75% of the pressure loss assigned to the main oxidizer shut-off valve can be used for additional pressure losses for other components in the recirculation chill-down system of a launch vehicle.
Keywords:
Main Oxidizer Shut-off Valve, Recirculation Chill-down System, Flow Coefficient, Liquid Rocket Engine키워드:
연소기 산화제 개폐밸브, 재순환예냉 시스템, 유량계수, 액체로켓엔진1. 서 론
발사체용 액체추진기관에는 연소기 및 가스발생기 혹은 예연소기 내에서의 연소 및 연소 중단을 위해 산화제와 연료의 공급과 차단이 원활히 이루어져야 하며, 다양한 종류의 개폐밸브가 추진제 공급과 차단 역할을 수행한다. 이러한 개폐밸브들은 상당한 고압 환경에서 작동되어지는 공통점은 있지만, 극저온 환경과 함께 고유량 조건에서 운용된다는 점에서 추진제 공급시스템에 설치되는 여러 개폐밸브 중에서도 연소기 산화제 개폐밸브의 역할이 매우 중요하다고 볼 수 있다[1-4].
더욱이 대부분의 개폐밸브들이 단순히 개방과 닫힘 작동을 통해 추진제의 공급과 차단이 이뤄지는 방식인데 비하여, 연소기 산화제 개폐밸브는 엔진 시동 점화 이전에 산화제 공급시스템의 예냉을 수행하기 위해 연소기로 통하는 밸브 출구 배관 이외에 재순환예냉 유로를 갖추어야 한다. 결국 연소기 산화제 개폐밸브는 두 방향 출구를 가지는, 일종의 3방향(3-way) 방식의 밸브라고 볼 수 있다. 발사체용 밸브는 무게와 크기 조건이 엄격히 제한되기 때문에 각 유로로 충분한 유량을 확보하면서도 동시에 밸브의 크기와 무게를 최소화하여 설계하여야 한다.
본 논문에서는 재순환예냉 유로의 유량계수에 초점을 맞춰 관련 연구내용과 설계 방향에 대한 내용을 소개하기로 한다. 우선 2절에서는 재순환 예냉 유로의 전반적인 특성 및 유량계수관련 설계 내용을 소개하며, 3절에서는 연소기 산화제 개폐밸브 재순환예냉 유로의 유량계수 개선에 대한 내용을 다루기로 한다.
2. 재순환예냉
2.1 재순환예냉 시스템
엔진 시동 점화 이전부터 액체추진기관의 엔진 및 산화제 공급라인은 예냉을 위해 액체산소로 채워지게 된다. 외부로부터 전달되는 열과 압력 조건에 의해 공급시스템 내부에서 산화제가 끓는점 이상으로 온도가 상승하여 기화될 수 있으며, 기화 된 기포에 의해 엔진 및 산화제 공급시스템에 수격 및 geyser 현상이 발생할 수 있다[5]. 이와 같은 위험한 상황을 피하기 위해 재순환예냉 시스템을 이용한 지속적인 액체산소의 순환 공급을 통해 액체추진기관의 연소기 산화제 개폐밸브 전단까지의 산화제 공급시스템 내부를 예냉하게 된다. 재순환예냉 시스템은 Fig. 1에서와 같이 산화제 추진제 탱크와 엔진과 연결되는, 순환 형태의 배관과 연소기 산화제 개폐밸브의 재순환예냉 포트 후단에서 헬륨 가스를 주입할 수 있는 배관 시스템으로 이루어져 있다.
재순환예냉 시스템의 목적은 엔진의 산화제 펌프 입구 온도 Tin을 엔진 시동 점화전까지 요구조건에 맞게 유지하는 것으로써 Tin 다음과 같은 예측할 수 있다.
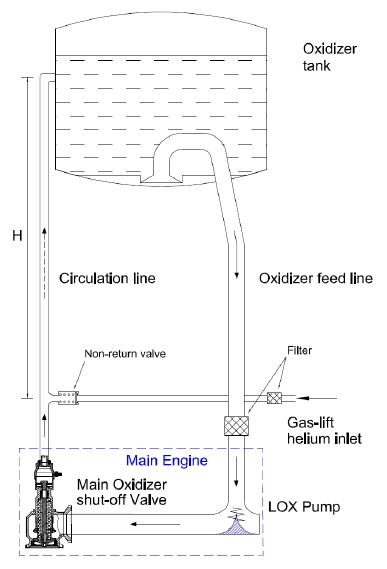
Chill-down system diagram for a launch vehicle (solid line arrow: LOX flow, dashed line arrow: gasified flow).
(1) |
여기서 Tt는 추진제 탱크 출구에서의 온도를 의미하며, q와 S는 각각 추진제 공급배관의 단위 면적당 유입되는 열량과 전체 배관의 표면적을 나타낸다. 한편, cp와 는 각각 액체산소의 비열과 질유량을 의미한다. 한편, Eq. 1에서 액체산소 질유량은 재순환예냉 시스템 내의 운용유체의 밀도차에 의해 발생하는 압력차로 얻어지는 유속 υ으로부터 예측할 수 있는데, υ는 다음과 같은 차압 관계로부터 계산할 수 있다.
(2) |
여기서 ξ는 압력손실계수이며, ρlox과 ρmix는 각각 액체산소와 헬륨 주입 후 혼합된 액체-기체 이상유체의 밀도를 의미한다. H는 Fig. 1에서와 같이 재순환라인의 수직 높이를 나타낸다. 따라서 액체산소의 유속은 다음과 같다.
(3) |
따라서, 재순환라인에서의 액체산소 유량 은 다음과 같다.
(4) |
여기서 A는 재순환예냉 유로 단면적을 의미한다. 재순환예냉 유로의 유량은 Eq. 1의 열유량 조건을 만족하여야 하는데, 일반적으로 일정 온도 이하로 요구되는 Tin을 만족하기 위해서는 가능한 많은 양의 액체산소를 순환시키는 방향으로 설계하여야 하며, Eq. 4에서와 같이 재순환예냉 시스템의 전체 유량저항계수 ξ를 낮추는 것이 유리하다. 결과적으로 발사체 시스템 설계 단계에서 재순환예냉의 유연한 설계 폭을 가져가기 위해서는 최대한 낮은 ξ를 가지도록 설계하여야 한다는 것이다.
한편 재순환예냉 시스템을 구성하는 각 부품이 유량을 흘러 보내는 정도는 유량계수 Kυ를 사용하여 일반적으로 다음과 같이 정의한다.
(5) |
여기서 Q는 시간당 흐른 운용유체의 부피유량(m3)을 의미하며 ∆p는 부품 양단에 걸리는 압력차로써 본 논문에서는 1 bar 단위압력 조건을 사용한다. G는 운용유체의 비중을 의미한다. 논문에서의 Kυ는 해당 부품 입출구 양단에 1 bar의 차압을 걸었을 때 3.6초 동안 흐른 유체의 ml 부피를 의미한다. 운용유체의 밀도가 일정할 경우, 유공압 부품의 유량계수 Kυ는 ξ-1/2에 비례하기 때문에[6,7], 결국 연소기 산화제 개폐밸브의 재순환라인으로의 Kυ를 증가시키는 방향으로 설계되어야 한다.
재순환예냉 시스템의 전체 유량계수 Kυ를 일렬로 연결된 차압들의 총합이라는 개념으로부터 다음과 같이 계산할 수 있다.
(6) |
따라서 단위 차압에 의한 유량을 증가시키기 위해서는 재순환예냉 시스템을 구성하는 각 구성품들의 유량계수를 크게 증가시킬 필요가 있다. Eq. 6에서 볼 수 있듯이 유량계수 차이가 큰 구성품들로 시스템이 구성되어 있는 경우, 전체 시스템의 유량계수는 시스템 구성품들 중에서 유량계수가 가장 작은 구성품의 유량계수에 의해 크게 좌우된다. 이러한 점에서 재순환예냉 시스템의 유량계수는 Fig. 1에서 도시된 구성품 중에서 상대적으로 유로가 복잡하고 유로면적 또한 상대적으로 좁은 산화제 펌프와 연소기 산화제 개폐밸브의 유량계수에 의해 상당부분 결정된다는 것을 짐작할 수 있다. 따라서 재순환예냉 시스템의 유량계수를 증가시킬 수 있는 효과적인 방법으로써, 재순환예냉 시스템의 구성품 중에서 상대적으로 유량계수가 작은 연소기 산화제 개폐밸브의 재순환예냉 유로의 유량계수를 높이는 것이라고 볼 수 있다.
2.2 재순환예냉 유로 유량계수 예측
재순환예냉 유로와 관련하여 연소기 산화제 개폐밸브의 외형 및 단면 형상은 Fig. 2에서 확인할 수 있다. 연소기 산화제 개폐밸브가 닫혀있는 상태에서 극저온의 산화제가 밸브 입구로 유입되어 밸브 내부의 포핏과 부쉬를 거쳐 재순환예냉 출구 포트와 연결된 재순환배관을 통해 추진제 탱크로 보내지게 된다(Fig. 1 참조).
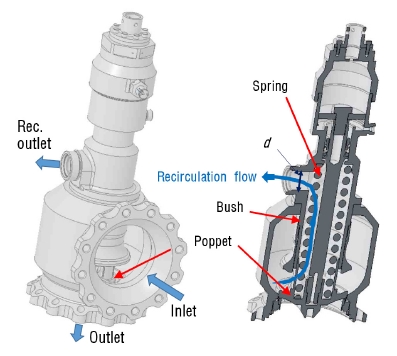
Configuration and sectional view for the recirculation chill-down flow line of Main Oxidizer shut-off Valve (d: recirculation outlet diameter).
새롭게 설계되는 연소기 산화제 개폐밸브의 유량계수를 예측하기 위해서 이전에 개발 제작된 연소기 산화제 개폐밸브로부터 측정한 재순환예냉 유로의 유량계수 값들을 이용할 수 있다. 재순환예냉 시스템 대신에 연소기 산화제 개폐밸브의 재순환예냉 유로의 총 유량계수를 Kυ라 하고, 재순환예냉 출구 전까지의 밸브 내부 부쉬 및 포핏 형상에 의해 결정되는 유량계수와 재순환예냉 포트 크기에 의해 결정되는 유량계수를 각각 Kα과 Kd라고 하면, Eq. 6과 같은 간단한 관계식으로부터 연소기 산화제 개폐밸브의 재순환예냉 유로의 유량계수 Kυ를 예측할 수 있다.
(7) |
재순환예냉 유로의 유량계수를 개선하려는 밸브의 재순환예냉 출구 포트의 크기를 결정하기 위해서 우선 재순환예냉 출구 포트 지름 d의 증가에 따른 Kυ 변화에 대한 예측이 필요하다. 밸브 내부 및 포핏의 형상이 동일하고(Kα가 동일), 재순환예냉 출구 포트 지름이 각각 22.35 mm와 17.6 mm인 이전 연소기 산화제 개폐밸브의 유량계수 측정값은 각각 11과 7.78로 측정되었다[8]. Kd는 재순환예냉 출구 포트 지름 d2에 비례하기 때문에 Eq. 7로부터 밸브 내부 형상에 의해 결정되는 Kd의 값 17.94를 얻을 수 있다. 또한 재순환예냉 포트 지름이 22.35 mm와 17.6 mm의 유량계수 Kd는 각각 13.92와 8.63으로 계산된다. 따라서 재순환예냉 출구 포트의 지름이 d인 연소기 산화제 개폐밸브의 Kυ는 다음과 같이 예측할 수 있다.
(8) |
여기서, d의 단위는 mm이다. α는 밸브 내부 부쉬 및 포핏 형상 변화에 따른 Kα의 변화를 나타낸 가중치이다. α가 1보다 큰 경우, 밸브 내부 형상 변화로 인해 밸브 차압이 감소한 경우를, 즉 Kα이 증가한 경우를 의미한다. Fig. 3에서 새롭게 설계되는 연소기 산화제 개폐밸브에 대한 재순환예냉 유로의 유량계수 예측값을 확인할 수 있는데, 그래프에서 실선은 밸브 내부 및 포핏의 형상이 이전 밸브와 동일한 경우이며(α = 1), 점선은 밸브 내부 및 포핏 형상이 변화되어 Kα이 증가한 경우를 나타낸다. Fig. 3에서 볼 수 있듯이, 밸브 내부 및 포핏 형상에 변경에 의해 Kα이 기존에 비해 증가될 경우, 같은 d의 경우에 대해 연소기 산화제 개폐밸브의 재순환예냉 유로의 총 유량계수 Kυ 또한 Kα과 비례해서 효과적으로 증가하는 것을 확인할 수 있다.
3. 유량계수 개선
3.1 밸브 내부 형상 및 재순환예냉 포트 크기 변경
밸브 크기 및 무게에 대한 제한조건과 재순환예냉 배관과의 체결성을 고려하여 새로운 밸브의 재순환예냉 포트 출구의 지름을 최종적으로 28 mm로 확대하였는데, 이 경우 Fig. 3에서 볼 수 있듯이 밸브 내부 형상에 변화가 없을 경우 (α = 1), Kυ가 14 가량으로 높아질 것으로 예측된다. 한편 재순환예냉 유로 유량계수의 보다 효과적인 개선을 위한 방안으로 밸브 내부 부쉬 형상에 의해 결정되는 유량계수 Kα를 향상시키기 위해 밸브 내부 형상을 개선하였는데, 해당 내용은 Fig. 4에서 확인할 수 있다. 이전 밸브의 부쉬 중간 부위에 있었던 스프링 지지대를 제거하고, 부쉬 내부를 긴 원통으로 단순한 형태로 변경하여 밸브 내부의 재순환예냉 유로에 걸리는 차압을 감소시키려 하였다. 한편 밸브 내부 부쉬 변경과 관련하여 중요한 점은 이러한 변경이 부쉬 자체만의 단순한 변경을 의미하는 것이 아니라, 부쉬 형태 변경과 복잡하게 얽혀있는 다른 부분들 즉 스프링, 밸브 힘평형 등 밸브의 주요 설계 변경과도 깊숙이 연관되어져 있다는 것이다. 따라서 재순환예냉 유로의 유량계수 개선을 위해서 스프링 재선정 등 밸브의 전반적인 설계 또한 실제적인 변경이 이루어졌다.
3.2 액체질소를 이용한 유량계수 측정
우선 액체질소를 사용한 극저온 환경에서의 유량계수를 측정하였다. Fig. 5에서 극저온 환경에서의 시험 모습을 확인할 수 있으며, 밸브 입구 전단과 재순환예냉 출구 포트 후단에서 각각 배관 내부 유로 지름의 1배와 3배가 되는 위치에 압력포트를 설치하여 두 측정 지점사이의 차압(pin - pout)을 Honeywell사의 STD830 차압센서로 측정하였으며, 해당 센서의 차압 측정 오차는 1 mbar 이내이다. 한편 액체질소의 질유량을 Mircomotion사의 CMF 100M 질량유량계로 측정하였으며, 질유량 측정오차는 ±0.1%이다.
극저온 환경에서의 연소기 산화제 개폐밸브 재순환예냉 유로의 유량계수 측정 결과는 Fig. 6에 나타내었다. 액체질소 유량이 안정되게 흐르는 50~55초 구간과 80~85초 구간에서의 유량계수를 계산하였다. Fig. 6에서와 같이 해당 구간에서 측정된 밸브 입구 압력과 재순환예냉 유로에서의 온도 측정결과로부터 액체질소의 밀도를 구하여 유량계수를 측정하였는데, 두 구간에서 측정된 유량계수는 각각 16.9와 16.8이였다. Fig. 3(+기호)에서 볼 수 있듯이, 측정된 유량계수 값으로부터 새롭게 설계 제작된 연소기 산화제 개폐밸브 내부 형상에 의해 결정되는 유량계수 Kα가 기존 밸브에 비해 대략 50%가량 향상된 것으로 예측할 수 있다. Fig. 4에서 보는 바와 같이 기존 밸브의 형상에 비해 설계가 변경된 밸브의 내부 유로 형상이 상대적으로 단순화 된 것을 볼 수 있으며, 밸브 내부 유로의 이러한 형상 개선을 통해 유량계수가 50%가량 향상되었다고 볼 수 있다.
한편 연소기 산화제 개폐밸브 재순환예냉 유로의 차압 및 질유량 설계 요구조건은 각각 1.1 bar와 2.7 kg/s로써, 유량계수의 설계 요구값은 8.66이다. 새롭게 설계된 밸브의 경우, 재순환예냉 유로의 유량계수가 설계 요구조건 대비 2배 수준으로 증가하였기 때문에, 재순환예냉 시스템 설계에서의 연소기 산화제 개폐밸브에 할당되어 있는 설계 차압을 25% 수준으로 줄일 수 있는 이점을 가지게 되었다.
4. 결 론
극저온 추진제를 사용하는 액체추진기관의 예냉 시스템 설계의 유연성을 확보하기 위한 연소기 산화제 개폐밸브 재순환예냉 유로의 유량계수 개선 내용을 소개하였다. 추가적인 전산수치서 측정한 재순환예냉 유로의 유량계수 값들로부터 재순환예냉 포트 크기와 밸브 내부 유로 해석없이 간단한 수식을 활용하여, 기존 밸브에형상 변경에 의한 재순환예냉 유로의 유량계수 값을 예측하였으며, 액체질소를 사용한 극저온 환경에서 유량계수를 측정하여 예측값과의 비교를 통해 밸브 내부 형상 변경에 의한 유량계수 개선 정도를 확인하였다. 새롭게 설계 제작된 연소기 산화제 개폐밸브의 재순환예냉 유로의 유량계수는 기존 밸브에 비해 2배가량 향상되었으며, 결과적으로 연소기 산화제 개폐밸브에 배분되었던 설계 요구 차압의 75%가량을 재순환예냉 시스템에서 추가적으로 소요될 수 있는 잠재적인 차압 및 재순환예냉 시스템의 다른 구성품의 추가 차압으로 활용될 수 있게 되었다.
References
- Jeon, J., Hong, M., Kim, H., and Lee, S.Y., “A Study on the Force Balance of a Main Oxidizer shutoff Valve”, Journal of the Korean Society of Aeronautical & Space Sciences, 37(8), p812-818, (2009).
- Park, H., Bae, Y., Jang, K., Lee, S., Hong, M., and Lee, S.Y., “Development of a Main Oxidizer Shut-off Valve for Liquid Rocket Engine“, 60th International Astronautical Congress, Daejeon, Korea, Oct.), (2009.
- Lee, H., and Hong, M., “On the Valve Travel of a Main Oxidizer Shut-off Valve“, 5th International Symposium on Fluid Machinery and Fluids Engineering, Jeju, Korea, Oct.), (2012.
-
Kim, D., Hong, M., Park, J., and Lee, S.Y., “Study for the Development of a Main Oxidizer Shut-off Valve for Liquid Rocket Engines“, Journal of the Korean Society of Propulsion Engineers, 17(6), p113-119, (2013).
[https://doi.org/10.6108/kspe.2013.17.6.113]
- Filina, N.N., and Wesend II, J, G., Cryogenic two-phase flow: Applications to large-scale systems, Cambridge University Press, (2010).
- Hong., M., “On the Discharge Coefficient, Cd,“ KARI-PCT-TM-2006-016, (2006).
- Hong, M., “Study on the Improvement in Cv of a Main Oxidizer shut-off Valve“, Aerospace Engineering and Technology, 8(2), p140-148, (2009).
- Hong., M., “02. Report on Specifications (Main Oxidizer Shut-off Valve for KRE-075-002G engine),“ KARI-IDMS, L2-ES-00466, (2016).